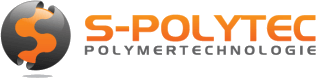
Building foam is versatile and is suitable for sealing, filling, bonding, insulating and insulating. Buy building foam at low prices and benefit from our selection of high-quality1C PU gun foaming , as well asCleaners and PU foam gunsfor easy and clean dosing of building foam.
Incl. 19% Tax
Incl. 19% Tax
Incl. 19% Tax
Incl. 19% Tax
Incl. 19% Tax
Incl. 19% Tax
Incl. 19% Tax
Building foam is extremely popular when it comes to effective sealing and insulating penetrations and joints. PU foams are used above all when installing windows and doors indoors and outdoors, as they achieve a heat-insulating and sound-insulating effect due to their cell structure. Processing is quick and easy, so that thermal bridges can be prevented in just a few steps. However, building foam is not only suitable for filling cavities, but can also be used very well as an adhesive. A proven example from practice is the bonding of insulation boards on the exterior façade.
The application possibilities for construction foam are enormously wide-ranging, so that we also stock targeted construction foams for special areas of application that are adapted to the particular requirements. For the bonding of exterior façade insulation, for example, a special 1C PU adhesive foam is available, which is characterised on the one hand by high adhesive strength and on the other hand requires very short waiting times until curing. For the installation of fire doors, smoke extraction systems or for sealing fire-relevant wall openings, we have a special 1C PU fire protection foam that is classified as flame-retardant according to DIN 4102 B1. For the installation of interior doors, windows or for filling joints and wall penetrations, a simple 1C PU gun foam is sufficient in most cases, so that we also have a suitable construction foam in our product range for such applications.
All PU gun foams available in the shop are classified as particularly low-emission to ensure a healthy living environment. Depending on the brand and manufacturer, different certification bodies come into play here. For some, the classification according to Emissions dans l'air intérieur is given the top grade A+. For other foams, the rating according to GEV-EMICODE is class EC1+ (very low emission). Detailed information on the emission ratings can therefore be found on the product page for each PU foam.
We also offer high-quality PU foam and gun cleaners to match the construction foams.
Building foam is a very sticky, tough mass that is difficult to remove. To clean contact surfaces from uncured foam, or to clean the foam guns after use, we offer special PU cleaners. These can simply be screwed onto the gun's receptacle and clean the gun's pipe system effectively and thoroughly. This ensures that residual building foam inside the gun does not harden and the gun can continue to be used. An adapter tube also allows cleaning of all surfaces to which PU foam adheres and is to be removed.
In order to be able to process building foam in gun cans, a PU foam gun is required. In case this is not yet available, we offer PU guns in various designs ranging from the inexpensive version for occasional use to the professional foam gun with adjustable adjustment wheel for precise dosing of the building foam, which is fully PTFE-coated both inside and out.
Before working with construction foam, ensure that there is sufficient ventilation. Protective gloves are compulsory in any case. It is also advisable to wear clothing that completely covers the skin!
Step 1:Shake
Building foam consists of a viscous mass and a blowing agent. These two ingredients must be mixed together properly. To do this, the foam can must be shaken vigorously for at least 15 seconds. Shaking creates the necessary pressure that transports the construction foam out of the can and causes the viscous liquid to dissolve. Only through sufficient shaking can sufficient expansion and formation of the fine-pored cell structure of the foam be achieved.
Step 2:Screw on
Before the construction foam can be applied, the can lid of the foam can must be removed. For single-component gun foam, the foam can must be screwed onto the foam gun. The valve should point upwards. However, do not screw too tightly, because after tight comes off. Hand-tight is sufficient here. Foam cans that are supplied with an adapter tube do not require a foam gun, so only the adapter needs to be screwed onto the valve.
Step 3:Apply
The foam is applied upside down, regardless of whether a foam gun or an adapter tube is used. Unlike spray adhesive, there is no riser tube inside the foam can, as installation foam is far too viscous, so the tube would quickly become blocked. In order for the foam to sink down through the valve and the can to be completely emptied, the can must therefore be held with the valve pointing downwards. To dispense the foam, the tip of the dispensing gun should be inserted as deeply as possible. Apply the construction foam carefully and remember that it will still swell. Although you can still cut off excess foam after it has cured, too much is not helpful either. In the case of very dry building materials that absorb moisture (e.g. plaster, sand-lime brick, etc.), it is advisable to moisten the surfaces with water beforehand.
Step 4: Moisturising
After application, the construction foam should be moistened with water, as it needs sufficient moisture to swell and harden. The surfaces of the foam can be easily and precisely wetted with a commercially available spray gun. 2-component PU foam contains an additional activator that acts as a hardener and sets a chemical reaction in motion. With such foams, additional moistening of the surfaces is not necessary.
Step 5:Wait
If construction foam is used for sealing, filling, insulating or insulating, the freshly applied foam must harden. To do this, the installation foam needs moisture, as described in step 4, and time. How long the foam has to cure depends on the type of construction foam. With fast-curing foams, curing is completed within a few minutes. With one-component standard foams, it sometimes takes five to eight hours before they are completely cured. In addition, the layer thickness of the application is also decisive for the waiting time until the foam has reached its final strength.
Step 6:Cut
After the installation foam has cured, any overflowing material can be cut with a sharp knife if necessary and thus easily removed. An ordinary cutter knife with a wide blade is perfectly suited for this purpose, as the sharp snap-off blade allows it to glide effortlessly through the hardened construction foam and ensures a precise, straight cut.
NOTE:As with all adhesives and sealants, the substrates must be clean and free of dust and grease before applying the PU foam in order to achieve optimum adhesion.
Installation foam is a versatile adhesive used for bonding, insulating and filling. Installation foam is particularly popular for installing windows and door frames. In addition, installation foam is also used for bonding insulation boards, filling cables and ventilation ducts in masonry, or for gap-filling insulation in attic conversions. This is a viscous adhesive, usually based on polyurethane, which foams up in combination with a blowing agent. For this reason, product names such as PU foam or PUR foam are very common colloquially. A distinction is made between ready-to-use single-component PU foams, which harden through moisture, and two-component assembly foams, in which an additional activator (or hardener) causes the hardening.
1C assembly foams are among the most commonly used foams in the construction industry and trade and account for around 80% of the market share for assembly foams in this country, which is why they are often also referred to as tree foam. These are usually aerosol cans that contain the ready-to-use PU foam along with a blowing agent. The components are mixed by shaking the foam can vigorously, which causes the material to escape from the can and foam up. This process is often called foaming. Depending on the design of the aerosol can, a foam gun or a hand dispenser is required for application, which is screwed onto the can in order to achieve targeted dosing of the assembly foam. How much the foam foams depends on various factors. The foam quality is influenced on the one hand by whether the components have been sufficiently mixed by shaking, and on the other hand by the ambient temperature. In addition, the relative humidity is decisive, because one-component PU foams need moisture to initiate the curing reaction.
At first glance, two-component assembly foams are in most cases indistinguishable from single-component foams, as these are also available in a foam can. The essential difference, however, is that this can contains an additional hardener, which is located in a separate container or a second chamber inside the can. As the foam comes out, the hardener is mixed with the foam, initiating the chemical reaction for curing. The biggest advantage of chemical curing is that it cures much faster without the humidity and ambient temperature affecting the foam quality. Additional humidification or high air humidity is not necessary with 2-component PU foam - on the contrary. If a two-component construction foam is used, the substrate must be absolutely dry.
Not all building foam is the same. Starting with the many common names such as assembly foam, PU foam, PUR foam, all of which are generally used for conventional construction foam, there are also special types of foam that have been developed for specific purposes. In most cases, however, the properties of the special foams differ only slightly, so that the simple 1C PU foam can be used. It is not for nothing that this makes up a market share of around 80% in construction foam.
1C PU foam
The largest share of the construction foam market is made up of simple 1C PU foam or 1C PUR foam. This also forms the basis for most other types of foam. This is a viscous mass of polyurethane and a blowing agent. PU foam adheres to almost all building materials and requires moisture to cure. Another chemical component, as in the case of 2-component PU foam, is not required for the foam to become solid. The working temperature of PU foam is between +5°C and about +30°C. After curing, however, PU foam is quite frost-resistant. The temperature resistance of most building foams ranges from about -40°C to about +80°C after curing.
2C PU foam
2C PU foam is a construction foam that, in addition to the actual PU foam and the blowing agent, contains an activator or hardener in a separate container that initiates the hardening of the foam through a chemical reaction of the components. In most 2C foams, the separate hardener is integrated in the aerosol can, so that these foam cans can also be processed with conventional foam guns. These foams are significantly harder and do not require moisture for curing. In addition, a 2C PU foam cures within a few minutes, which significantly reduces waiting times until cut resistance.
Window foam
When installing window profiles made of aluminium, wood or PVC plastic, a window foam achieves very good sound insulation and improved thermal insulation. As the window profiles expand due to solar radiation, a window foam is more elastic and can be compressed more easily when the profiles expand due to heat. Even though a window foam helps to fix the window frame, the profiles must also be statically anchored. Moreover, window foam does not serve to seal the cavities watertight, so that the wall connection joints must subsequently be protected and sealed against rain and water logging with a suitable silicone sealant.
Frame foam
Frame foam, as the name suggests, is used to assemble door frames. A good door frame foam is characterised by a higher density, which results in better strength. In addition, the higher density also results in better thermal insulation. If the space between the masonry and the frame is completely filled with foam, this also results in significantly better sound insulation. Since the air circulation is not optimal after inserting the frame, and thus there is not enough moisture for the foam to cure, most frame foams are two-component systems that cure chemically. Another advantage of 2-component frame foam is that the door frame only needs to be spread with struts for a short time so that the expanding foam does not bulge the frame inwards.
Adhesive foam
An adhesive foam is often used for bonding insulation boards, plasterboard or fibreboard because they harden much faster than conventional PU foam and usually also have a higher tensile strength. In addition, a strong expansion, as with filling foam, is not desired with an adhesive foam. Especially when bonding insulation boards, an even better insulation value is achieved with adhesive foam, as the adhesive foam also contributes to increasing the thermal resistance.
Fire protection foam
Fire protection foam owes its name to its flame-retardant properties, which must be fulfilled according to DIN 4102 B1. Conventional construction foam is normally flammable and completely unsuitable for foaming fire doors, ventilation systems or smoke extraction systems. Flame-retardant fire protection foam can be used in construction areas with special fire behaviour requirements for the demarcation of fire protection sections.
Winter foam
Winter foam is a special foam which, in contrast to other types of foam, can also be used at temperatures below zero. The lowest temperatures for processing range from -10°C to -20°C, depending on the manufacturer. At low temperatures, the humidity is lower, which prolongs the curing time of conventional foams. This results in poorer foam quality with conventional foams, which also results in poorer heat and sound insulation. This problem does not exist with winter foam, so that it can also be used on construction sites in winter. In order for the foam to be dispensed, however, the foam can should have an intrinsic temperature of at least +5°C, otherwise the PU mass in the can is too viscous and can thus hardly be applied properly.
Well foam
Well foam is mainly used in civil engineering for sealing concrete shaft rings, sewage pipes or well shafts. This special foam is waterproof, but this does not mean that it is also watertight. The tightness is achieved by the high contact pressure of the individual manhole rings. In some cases, the joints are additionally sealed with a silicone sealant after the well foam has been cut. Well foam is resistant to rotting and decay, but is not suitable for pipes carrying drinking water, wells and cisterns.
Filling foam
Filling foam is usually just a simple 1K PU foam. In most cases, the product name is meant to mislead you into thinking that it is a special foam specifically for filling holes and wall penetrations. A good filling foam has good adhesion to most substrates, is easy to apply and foams up more to penetrate into tight joints and cracks.
MDI-reduced foam
Most construction foams are isocyanate-containing foams that contain methyl diphenyl isocyanate. These so-called MDIs are considered to be potentially carcinogenic when the construction foam is not cured. After the foam has fully cured, however, the risk no longer exists. In MDI-reduced foams, the content of free isocyanates is reduced. A distinction is made here between moderately reduced foams with a maximum MDI content of 1% and strongly reduced foams with less than 0.1% MDI. In addition, MDI-free foams are also available, which no longer contain any free isocyanate groups and split off methanol during cross-linking.
To remove building foam, one should not wait long, because as long as the foam has not yet hardened, it can still be removed from surfaces quite well. If this means having to interrupt the work, you should take your time, because the more time that passes, the harder it will be to get rid of the PU foam without leaving any residue. A special PU foam cleaner is the most effective way to remove the sticky mass completely. First remove the foam roughly with some kitchen roll. The next step is to apply the cleaner and remove the residue adhering to the surface with a clean cloth or kitchen roll. To ensure that the cleaner does not attack the surfaces, the compatibility should be tested on an inconspicuous area beforehand. Wearing gloves is always a must with building foam. Also when cleaning surfaces and tools.
If no PU foam cleaner is available, PU foam can also be removed with standard vegetable oil and a soft cloth. However, this creates an oil film on the surface, which must then be removed in a further cleaning step. This is particularly important if building foam or a silicone for sealing joints is to be applied to the surface again later. Cosmetic wipes from the drugstore are also very suitable for quick removal. Baby wipes containing oil are particularly effective here.
Tools and foam guns should always be cleaned immediately after use. Especially in the case of simple models that do not have a high-quality non-stick Teflon coating, too long a delay can result in sticking inside the gun barrel. This means that the gun has only scrap value and is out of the question for further use. High-quality models are equipped with a Teflon coating in the inner tube. Professional models for manual use are usually even completely coated with Teflon, so that they are much easier to clean. For cleaning, a gun cleaner is usually used, which is screwed onto the gun. By operating the handle lever, the complete pipe system is flushed and thoroughly cleaned. To clean the tool surfaces, the cleaner can be applied to a cloth and the impurities lightly rubbed off.
Once the construction foam has hardened, it is usually almost impossible to remove it without leaving residues. The only way to remove it is mechanically by cutting it out with a knife or scraping off foam residues with a profile scraper. However, you should be extremely careful here so as not to damage the surfaces. More sensitive surfaces such as wooden door frames or plastic window profiles should be cleaned with a scouring pad and a little soap solution. This may be tedious, but it prevents unsightly scratches in the window frame.
PU foam is basically harmless if personal protective equipment is worn during processing and the construction foam is only used in well-ventilated rooms. Once the construction foam has completely hardened, there is no longer any danger from this adhesive and sealant.
PU foam contains isocyanates, which are generally classified as risk substances because they can cause eye irritation, skin irritation and respiratory tract irritation. In single-component PU foam, methyl diphenyl isocyanate (MDI for short) is very often used. Tree foams with an MDI content of more than 1% are suspected of being carcinogenic. Concrete evidence of a carcinogenic effect is not yet known, but an increased cancer rate was found in animal experiments when the poor animal was exposed to respirable MDI. The presumed carcinogenic effect relates to the inhalation of aerosols released during the processing and curing of the foam. Once the foam has cured, no respirable forms of isocyanates are released into the air, or the amount is so low that it no longer poses a risk.
As mentioned at the beginning, building foam has a strong irritating effect on the skin and mucous membranes, which is further intensified by the high stickiness of the foam. However, this only applies to building foam in an uncured state, so gloves and protective goggles should be worn when working with it. When working with construction foam, it is advisable to wear long clothing that covers the body completely. In addition, good ventilation should be ensured when dosing the foam until final curing. After curing, however, the PU foam no longer has an irritating effect.
When disposing of used foam cans, a distinction must be made between cured foam and the foam cans, because used foam cans are classified as hazardous waste due to the remaining ingredients as well as the pressurised gas packaging and must be treated as such. This means that used foam cans, whether they are opened or empty, must be disposed of at appropriate collection points. Even empty cans still contain small residual amounts of the PU foam or the blowing agent, so that disposal via household waste or the yellow bag is not permitted. The situation is different for construction foam in its hardened state, because it is neutral to the environment and can therefore be disposed of in the residual waste without any problems.