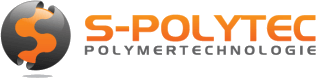
Buy MS polymers at best prices online at S-Polytec and benefit from the many advantages of the high-quality assembly adhesives that are equally suitable as sealants. Our MS polymers are UV-resistant, weatherproof and waterproof and are characterised by enormous initial adhesion and tensile strength on almost all materials, even without a primer.
Incl. 19% Tax
Incl. 19% Tax
Silicone is used to seal expansion joints or to prevent moisture penetration. An acrylic is used to fill cracks and joints that are to be painted over, and an adhesive that matches the material is used for bonding. All these areas of application can be covered with an MS polymer.
An MS polymer is a one-component, ready-to-use hybrid system that is equally suitable for bonding and sealing. The areas of application are very broad and MS polymers are used indoors as well as for outdoor applications. Starting with the quick and easy installation of cable ducts, which are glued instead of drilled, to the installation of ceiling panels and wall cladding without disturbing screw connections in the visible area, our MS polymer is excellently suited as an assembly adhesive. Thanks to its good elasticity, skirting boards made of tiles or wood can also be attached in no time at all and sealed in one step to achieve an airtight and watertight seal. Especially in furniture construction, an MS polymer is an outstanding alternative to conventional wood glue, especially when surfaces made of real wood are to be bonded to other materials such as metal or concrete. As a waterproof sealant, this all-rounder can even be used on damp surfaces. In pool construction or air-conditioning technology, MS polymers are often even used when the bonding points or sealants are permanently under water after curing. A silicone is usually only suitable to a limited extent for such purposes.
Another very popular area of application is vehicle construction. In times when range and efficiency are important, every gram of weight saved is of great importance. So nowadays, it is very often the case that body parts are not screwed together and are instead joined by using MS polymers in combination with the spot-welding process. This achieves an extremely durable connection of the body parts, even if these are not exclusively metal connections to each other, but mixed connections of metals and plastics.
MS polymers adhere to almost all surfaces and materials used in construction and industry. In most cases, there is no need for a primer as an adhesion promoter. However, MS polymers are not suitable for polyethylene, polypropylene or PTFE, because these plastics are so chemically innert that the assembly adhesive does not achieve sufficient adhesion to the surface. MS polymers should also not be used on EPDM, bitumen or neoprene, as well as on silicone or butyl rubber. For treated and untreated wood, tiles, ceramics, concrete, stone, plaster and metal and much more, however, an MS polymer is the perfect alternative to conventional fastening solutions and is also suitable for alloyed steels or sensitive surfaces such as natural stone.
MS polymers are hybrid systems and consist of modified silanes, which is where the abbreviation MS comes from. The main difference compared to conventional silicones is that the adhesion promoter is already contained in the sealant, so there is no need to apply a primer. This results in a universal hybrid adhesive and sealant that has excellent adhesion to most substrates. The easy processing of the one-component assembly adhesives is equivalent to the processing of silicones. Even for the application of an MS polymer, all that is needed is a sharp knife to cut open the cartridge and an applicator gun for standard cartridges.
Sealants based on silane-modified polymers are among the neutrally curing sealants that release alcohols during cross-linking by atmospheric humidity. An unpleasant, acrid vinegar smell, as is the case with Acatet systems, does not arise during curing. In addition, the neutral cross-linking means that MS polymers do not attack surfaces. The adhesive and sealant is therefore not only suitable without hesitation for natural stone, which is otherwise prone to edge discolouration on the sensitive surfaces. There is also no need to fear the formation of corrosion when bonding metals by using MS polymers.
Our MS polymers are free of harmful substances and plasticisers, so no phthalates, which are classified as hazardous to health, are released either before or after curing. Furthermore, our assembly adhesives are free of solvents and do not contain any isocyanates.
NOTE: Even though MS polymers do not attack surfaces, it is recommended to test the material on a test piece or on an inconspicuous spot to assess material compatibility and adhesion.
MS polymers are comparably easy to process as silicones or acrylics, but as hybrid adhesives they can convince with some advantages over conventional silicone sealants. Whereas silicones are mainly used for sealing and caulking and are only suitable for bonding with moderate weight loads, MS polymers are excellent assembly adhesives as adhesives and sealants, which are characterised by enormous initial adhesion to almost all surfaces even without the use of adhesion promoters. Therefore, bonding with an MS polymer is an excellent alternative to fastenings made by drilling and screwing.
The elastic sealants are in no way inferior to a good silicone in most aspects. Only the elongation at break of MS polymers is significantly lower than that of silicone sealants, so that for seals that are subject to high mechanical stress, it may be necessary to resort to a silicone. The reason for this is the higher shore hardness of the hybrid system, which is about three times higher compared to the shore hardness of cured silicone. Also due to the higher shore hardness, an MS polymer is much harder to remove after curing than a softer silicone joint. However, for bondings that are subject to long-lasting, high weight loads, this is an advantage worth mentioning, even if they are subject to constant movement. The more complex manufacturing process is also reflected in the price, as an MS polymer costs about half as much as a good neutral-cross-linking silicone sealant.
Like most silicones, MS polymers are also air- and water-tight after curing and are therefore very suitable for sealing joints and cracks. Weatherproof properties, such as UV resistance and resistance to weathering, such as frost, heat or acid rain, do not have to be foregone with an MS polymer either. The good ageing resistance contributes to the fact that there is no loss of quality due to cracks, deposits or loss of flank adhesion, even with continuous UV exposure. Thanks to the UV resistance, discolouration of the cured assembly adhesive through fading or yellowing is also not to be expected. A significant advantage, apart from the significantly higher adhesive strength, is that MS polymers can be painted over. Sealants, caulks or adhesives can be painted over with most dispersion-based paints. Even solvent-based paints and varnishes can be used to paint or varnish over the adhesive and sealant. Overpainting silicones, on the other hand, is not possible.
An MS polymer holds immediately thanks to its high initial adhesion and is often an excellent alternative to drilling. After curing, the elastic assembly adhesive even withstands mechanical stresses that can occur due to constant, repetitive movements. For adhesion, a distinction is made between tensile strength and tensile shear strength (shear strength).
The initial adhesion provides information on how strong the weight load must be immediately after bonding so that it can be withstood without the parts to be joined having to be fixed in place. With MS polymers, this exceeds the load-bearing capacity of conventional silicones many times over, which is why assembly adhesives are generally the better choice. The very high initial adhesion, which is often stated as "high-tack" in the product labelling of an MS polymer, sometimes varies significantly depending on the manufacturer. Adhesion specifications also vary. Some give the weight in grams per square centimetre, while other manufacturers use the unit of measurement kg/m². A uniform system would make it easier for the end user to know which mounting adhesive has sufficient initial adhesion for the project, but this is not standardised, so in case of doubt you have to do some maths to compare the values.
The final bond strength of an assembly adhesive refers to the load-bearing capacity of the bond after the adhesive has fully cured. Here, too, a distinction is made between tensile strength and tensile shear strength. While the tensile strength provides information on how much force must be exerted to release the bonded joint against the bond, the tensile shear strength indicates the forces that must be exerted for the bonded joint to release by displacement of the joined parts and is therefore often referred to as shear strength. These values not only vary depending on the materials being bonded, but also depend on the length of time that has passed since they were joined.
As already mentioned, the values provide little information without details of the bonded materials. With our MS polymers, the initial tensile strength in a tested text bonding of beech wood to each other is a very high 300g/cm². Converted, this results in an incredible 3000kg per square metre. After curing, the bond can withstand a tensile load of 24kg/cm². The shear strength immediately after bonding is 10g/cm², which increases to a very high value of 15kg/cm² after only 4 hours and reaches an extreme value of 32kg/cm² after curing. Our MS polymer can also convince with very good values when bonding aluminium to aluminium and reaches a tensile strength of 14kg/cm² already after a short time of 4 hours. In the test procedure, a final strength of 24kg/cm² could be determined for this bonding after a one-week period.
How much weight an assembly adhesive can support depends primarily on the initial adhesion and final adhesion of the adhesive. However, depending on the manufacturer, the load-bearing capacities vary greatly. Values of more than 10kg per square centimetre are not uncommon with MS polymers, however. In addition, the available bonding surface is also important. It should be noted that it is not the surface area of the materials to be bonded that is decisive, but the area occupied by the adhesive after the substrates have been joined. The larger this area and the greater the adhesion of the MS polymer to the material, the greater the weight that an assembly adhesive can hold permanently and securely.
The type of bonding also plays a relevant role, because with most adhesives, including MS polymers, the initial tensile strength is usually many times higher than the shear strength. If ceiling tiles are bonded flat under the ceiling, a tensile load acts on the bond that depends on the weight of the tile. If, on the other hand, the tiles are attached to the wall, the weight of the tile will contribute to the possibility of the tiles slipping downwards if the shear strength is lower than the weight of the tile. Even though our MS polymers can convince with very good values for tensile and tensile-shear strength, care should always be taken to ensure sufficient fixation until curing, especially if large or heavy panels are to be bonded, or the bond is subject to certain tensile loads due to radii or bends.
MS polymers cure through contact with atmospheric moisture. The curing speed depends on the moisture content of the ambient air and the prevailing temperatures.
The curing time depends on the thickness of the bond and is approx. 2.5-3.0mm in 24 hours at room temperature (23°C) and a relative humidity of 50%. Higher humidity can accelerate the curing. A lower percentage of relative humidity in the ambient air, on the other hand, can contribute to slower curing. The situation is similar at higher or lower temperatures. As a general rule, MS polymers should always be used in frost-free environments, as sub-zero temperatures can cause the freshly applied assembly adhesive to freeze before curing has occurred, making it impossible for the MS polymer to cross-link. In the worst case, this can contribute to the fact that the curing no longer takes place and thus a load-bearing bond cannot be guaranteed. Excessively high temperatures can in turn cause a significant acceleration of the cross-linking process. In this case, bonding can still take place, but depending on the temperature, haste is required. As soon as skin formation has set in, it is no longer possible to attach the desired objects without compromising the bonding in terms of load-bearing capacity. In this case, the mounting adhesive should be removed with a spatula and reapplied to ensure a permanent, secure bond.
NOTE: The ideal temperature range for processing MS polymers is between +5°C and +40°C. Bonding should not be carried out at temperatures below the zero degree mark or at excessively high temperatures. After curing, however, an MS polymer is absolutely frost-resistant down to -40°C and durable despite even high temperatures up to +90°C, without affecting the durability and quality of the bond.
To ensure cross-linking of the MS polymer, it should be ensured that the applied adhesive has sufficient contact with the surrounding humidity. Small bondings can easily be made in spots or by a linear application of the assembly adhesive. For large-area bonding, it is advisable to apply the MS polymer with many individual dots or in a wave form. A large-area or ring-shaped application, on the other hand, is not conducive, because the humidity in the air may not be able to reach all the bonded areas, which can significantly delay or even completely prevent curing.
CAUTION: If an MS polymer cannot cure or cannot cure sufficiently due to the lack of contact with the humidity in the air in the environment, this will affect the load-bearing capacity of the bond.
The shelf life of an MS polymer is usually 12 months from the date of filling. The shelf life of the adhesive joint, on the other hand, is not limited.
If bonding with an MS polymer is carried out professionally on suitable substrates, the bonded joint will normally last a lifetime. Even under mechanical stress caused by vibrations or movement, as well as permanent tensile stress, the bond will not come loose once the assembly adhesive has fully cured. It does not matter whether the adhesive is used indoors, for example when bonding mirrors, ceiling panelling or skirting boards, or whether the bonded area is permanently exposed to strong UV radiation, as can be the case with bonded facade cladding. As waterproof adhesives, MS polymers are even suitable for bonding on damp substrates and do not suffer any loss of quality if the bonded area is permanently submerged in water.
Unbroken carton boards or skirting boards are also suitable for bonding on damp substrates and do not suffer any loss of quality if the bonded area is permanently submerged in water.
Unopened cartridges of an MS polymer can be stored for up to twelve months under good storage conditions. However, the decisive factor is not the date of purchase or delivery, but the date on which the cartridge was filled. For most manufacturers, this date is printed on the upper edge of the cartridge. With our MS polymers, we also indicate the date until which the assembly adhesive can be used without hesitation. This is indicated by the abbreviation EXP and is also located on the top edge of the cartridge.
Single-component MS polymers in commercially available standard cartridges require similar storage conditions as silicones. Therefore, assembly adhesives should always be stored in a cool, frost-free place. The ideal storage temperature for sealed cartridges is between +5°C and +25°C. Temperatures below zero can significantly reduce the shelf life of MS polymers. Storage under prolonged, high heat exposure can also have a negative impact on shelf life.
TIP: Opened cartridges can certainly be stored. However, it is important to make sure that the cartridge is sealed airtight, because MS polymers react with humidity so that they harden. The easiest way to do this is to leave the cartridge tip screwed on and seal it with some cling film and tape to prevent air from getting to the assembly adhesive. A dry, cool storage location also has a positive effect on the shelf life of opened MS polymers.
Freshly applied MS polymer can be easily removed with a spatula or a lint-free cloth. However, this should be done before the adhesive has cured, because once an MS polymer has fully cured, it is difficult to remove. For this reason, these assembly adhesives should only be used if the bond is to be permanently maintained. The cured sealant can no longer be dissolved with solvents, so the bond can only be removed mechanically, for example with a sharp knife or saw. Our robust profile scrapers are also very suitable for removing adhesive residues from flat surfaces. Care should always be taken when doing so, because on the one hand, the use of sharp tools can cause a risk of injury and on the other hand, the surfaces can be damaged.
Excess, pre-swelling material should be removed immediately after attaching the joining parts. The tools used should also be cleaned immediately afterwards, if necessary, so that the silicone gun, spatula or similar can be easily removed from adhesions and adhesive residues.
MS polymers cannot be recycled, so thermal recycling, i.e. incineration of the assembly adhesive, is currently the only type of recycling. The same applies to cartridges that have not been completely emptied or still have adhesive residue on them. Although MS polymers are usually made from polypropylene, this plastic can only be recycled well if it is collected sorted by type and free of coarse impurities.