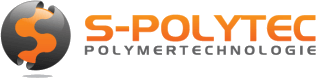
The right screw for every assembly. With our wood screws you are optimally equipped, regardless of whether they areto be used for direct screw fastening in woodand plastic or for assembly with dowels.
Incl. 19% Tax
Incl. 19% Tax
Incl. 19% Tax
Incl. 19% Tax
Incl. 19% Tax
Incl. 19% Tax
Incl. 19% Tax
Incl. 19% Tax
Screws are as versatile as the applications for which screws are used. With our chipboard screws from fischer, we offer the perfect screws for mounting directly in wood or plastic. For example, to fasten fittings or angles. In addition, chipboard screws are also ideal as dowel screws in combination with our dowel range.
In contrast to our facade screws or balcony screws, which are mainly used for mounting cladding panels on exterior facades and balcony surrounds, we offer the perfect fixing solution for every purpose with the fischer screw range. From small picture frames in the living room, to wall cupboards in the kitchen, to the installation of a patio roof or a garden shed made of solid wood. Thanks to the different lengths and diameters, as well as the different screw head shapes and thread variants, no wish remains unfulfilled with us.
Ever ordered a single screw online? - It's possible with us!
In contrast to the usual market packaging units, you can order the screws in our online shop according to your personal requirements. It does not matter whether you need a single screw, 36 or 1500 for your project. We deliver the screws in exactly the quantity you put in the shopping basket, instead of limiting the offer to individual boxes of 20, 50 or 200 pieces.
Maximum flexibility - fill FIXtainer according to your needs
In the standard delivery programme, we offer pre-sorted assortment boxes with anchor screws or sets consisting of screws with matching anchors from fischer. The FIXtainers, as they are called by the manufacturer, are compact, stackable and can be combined using a click system. This makes transport easier and always has the necessary assembly material to hand.
With the fischer FIXtainers in our shop, hardly any wish remains unfulfilled, because the manufacturer already offers numerous ranges for household and handicraft. However, we go one step further and offer you the possibility to fill the practical transport box as you wish. Simply choose the screws in any size and quantity. If required, add the appropriate dowels or drill bits and fill your individual assortment box as you like after delivery.
NOTE:The range is constantly being expanded. If your screw is not included, further screw sizes and designs are available on request at any time.
The fischer PowerFast II chipboard screws with countersunk head are ideal for flush surface installation in wood, but are also excellent as dowel screws when used with a suitable dowel (e.g. fischer DuoPower or fischer UX). The continuous thread extends to the screw head. The advantage is optimum force transmission over the entire screw-in depth, with increased resistance to tensile forces at the same time, compared to a screw with identical dimensions with a partial thread. The screws are also suitable for direct screwing of most of our plastic panels. Both with each other and for screwing to wood materials.
We stock the chipboard screws of the fischer PowerFast II series with full thread in various diameters and lengths, from short filigree wood screws to long, thick screws for heavy loads.
NOTE:Detailed information on the available sizes, as well as recommended dowels for mounting in walls and ceilings, can be found in the product description, as well as in the Additional Information tab, after selecting the screw size.
The fischer PowerFast II chipboard screws with countersunk head and partial thread are perfect for screwing the assembly part to the substrate without leaving a gap. Partially threaded screws are also ideally suited for constraint-free assembly due to the thread-free shank. The coarse thread with a large spiral angle not only significantly reduces the screwing time, but also requires less force when screwing. An advantage that is not only noticeable with long screws with a larger screw diameter.
Our product range includes the most common lengths with both full and partial threads. Screws with longer threads, on the other hand, are usually only available as partially threaded screws.
NOTE:Details of the available screw sizes, as well as the recommended anchors for secure installation, are listed in the product description and the additional information for the selected screw.
Chipboard screws with a half-round head, such as the fischer PowerFast, are ideal for fixing angles or metal fittings. This applies both when screwing metals into wood, or as a dowel screw for installation with suitable dowels in masonry and ceilings. The full thread, which extends over the entire length of the thread, distributes the tensile force over the entire screw-in depth.
Screws with a half-round head are also often called panhead screws. Due to the flat underside, fastening with high tightening torques is possible without the screw head sinking into the material, as is the case with countersunk screws. A washer can further increase the contact surface. This is proven, especially when screwing into soft wood or thin metal sheets.
The fischer PowerFast screws with half-round head are classic wood screws with coarse thread. The version with partial thread is perfectly suited to screw metal braces, angles or steel beams tightly to wooden substructures. When erecting the roof truss, panhead screws are used in combination with washers to screw the wooden beams together without gaps. The thread-free shank effectively prevents the formation of gaps between the components. When assembling plastics or metals without forcing, it is even very important that the threadless area corresponds at least to the material thickness of the assembly part.
Screws with a half-round head are versatile. For this reason, we also offer many different designs, starting with the diameter, through various screw lengths, to partially threaded and fully threaded screws with a half-round head.
NOTE:Details of the available screw sizes, as well as the recommended anchors for secure installation, are listed in the product description and the additional information for the selected screw.
Which screw is suitable for the respective area of application depends on various factors. Not only one criterion has to be considered, but the sum of all individual parameters decides whether a screw can withstand the load or whether it is not up to the load. It is therefore not enough to use only one thick screw for a heavy installation object if its length is not sufficient for the required anchoring depth.
The material of a screw provides information about its tensile strength in relation to its physical properties. This alone does not say anything about the load-bearing capacity of the screw, but the required core diameter of a screw can be calculated on the basis of the strength class. In addition, the strength class of a screw indicates the maximum torque with which it may be tightened. It is usually indicated on the head of the screw or on the packaging of the screw. The specification of the strength class contains two numerical values, separated by a dot. The first value stands for the tensile strength in Newton per square millimetre. The second numerical value stands for the yield strength, which provides information about the force at which the material deforms.
Tensile strength (in N/mm²) = value 1 Strength class x 100
For a dowel screw with strength class 4.8, the value before the point is needed for the tensile strength.
Tensile strength (in N/mm²) = 4 * 100 -> 400 N/mm²
If you want to calculate the weight in kilograms, you can divide the tensile strength value you just determined by 10, because one newton corresponds to 102 grams. In our example, this results in a load-bearing capacity of the material of about 40 kg per square millimetre. This value can now be used for the ideal core diameter of a screw.
The screw diameter for mounting an add-on part depends primarily on the weight to be carried. However, it is important to consider the material from which the screw is made, because the load-bearing capacities sometimes differ significantly. Chipboard screws made of stainless steel with a thread diameter of 6mm, for example, have a higher strength than comparable screws made of brass. Plastic screws, on the other hand, which are usually made of polyamide, offer much lower strength. Furthermore, the type of screw must also be taken into account. The more solid the construction of a screw with the same diameter, the more stable the screw itself is, which also affects the load capacity of a fastening. A threaded screw with a metric thread of size M6 is therefore more load-bearing than a wood construction screw of the same material with a thread diameter of 6mm.
Another aspect to consider when calculating the perfect bolt diameter is the number of bolts. If an assembly part with a total weight of 15kg is to be fastened with one screw, the screw diameter will be higher than if the 15kg has to be held by four or more screws. The lower the weight of a single fastening, the smaller the diameter of the screw can be selected.
For the screw diameter, we need the weight that the individual screw is subjected to and the load-bearing capacity of the screw material, which results from the tensile strength. For the concrete calculation, many parameters have to be taken into account, such as the hardness of the material, the tightening torques, the different loads, as well as their distribution, which act on the screw connection, the thickness of the mounting parts and, last but not least, the load-bearing capacity of the substrate on which the assembly takes place. Such calculations are very complicated and also take into account the design of the screw, the physical properties of the thread form and much more. Even with a theoretical diameter calculation based on the tensile strength of the material, a root calculation is necessary here. By calculating the area of a circle with the circle number Pi, the radius and the diameter of the thread core can be calculated. The height of both thread flanks must be added to the core diameter to obtain the nominal diameter of the thread.
To check the maximum weight a bolt can withstand, a much simplified formula can be used to calculate the bolt diameter based on the tensile strength of the bolt material and the weight of the assembly part. For this, the weight must first be converted from kilograms to newtons. Here, too, the formula can be simplified by multiplying the weight by a factor of 10.
Min. Ø screw (in mm) = max. weight (N) / (load capacity (N/mm²) * 0.15)
For an assembly part weighing 25 kilograms and a steel screw with a strength class of 4.8, the following formula results.
Min. Ø screw (in mm) = 250 / (400 * 0.15) -> 250 / 60 -> 4.1667
WARNING:This is a purely mathematical value that only provides information about how much weight the pure material can withstand. This means that a screw with a diameter of 4.5mm would theoretically be able to withstand a weight of 25kg. For the real load-bearing capacity of a fastening, the load-bearing capacity of the substrate as well as the load from tensile, transverse and oblique forces must also be calculated. As a rule, however, such a high weight is attached with larger screws and a load distribution over several fixings. To be absolutely sure which screws to use than to calculate the load-bearing capacity of the screw itself, the manufacturer's data sheets or ETA approvals should be consulted in advance, which usually contain extensive tables on the respective screw sizes.
The length of the screw is determined by the required anchorage depth and the depth of the attachment. The higher the anchorage depth, the greater the tensile and oblique forces that can act on the screw connection. Conversely, this means that with increasing loads, a longer screw should be selected for more hold. The transverse force, where the weight acts at right angles to the fastening, is almost irrelevant for the length of the screw. The only thing that counts here is the assembly weight, which should be less than the load capacity of the selected screw.
The required anchoring depth depends on factors such as the pull-out resistance or the elasticity of the screw. Whether a fully threaded or partially threaded screw is used must also be taken into account, because the thread friction value increases with increasing screw depth of the thread into the wood. The thread pitch and the height of the thread flanks also have an influence on the hold of the screw in the material, which ultimately decides whether the loads can be carried or whether a longer screw should be used. Due to the many parameters, the calculation of the screw length cannot be generalised. However, for the assembly of simple loads in the household, or for screwing wood materials together, a simplified formula can be used in which the screw-in depth corresponds to six times the screw diameter.
Screw length (in mm) = (Ø screw (in mm) * 6) + thickness of attachment (in mm)
When mounting an aluminium composite panel in 3mm thickness with a 6mm chipboard screw on a wooden substructure, the calculation looks as follows.
Screw length (in mm) = (6mm * 6) + 3mm -> 36mm + 3mm -> 39mm
WARNING:When screwing two wooden workpieces together, there is a risk of chipping or puncturing on the opposite side of the screw joint if the screw is chosen too long. Therefore, the screw length should be chosen so that the maximum length of the two materials is reduced by the thread diameter. If the screw connection is too short for the load, several screws or screws with a higher diameter can increase the load capacity of the screw connection. If two boards of pine with a thickness of 20mm each are to be screwed together with a 6mm screw, the maximum length of 40mm must be reduced by 6mm. This means that the screw should be approx. 34mm long.
NOTE:For fastenings with higher tensile forces, transverse forces or for assembly parts with a higher mounting thickness, it should always be checked on a case-by-case basis whether the screw is suitable for the application. Well-known manufacturers such as Fischer have product-related data sheets that provide information about the possible loads, as well as the screw-in depths or the maximum clamping ranges.
If the screws are used for fastening with plastic dowels, the thread length of the screw should always be chosen longer than the dowel. The thickness of the attachment part must also be taken into account here. When mounting a plastic cladding panel with a thickness of 3 mm with screws and dowels, dowels with a size of 6x40 mm can be used due to the low weight. A screw diameter of 4.5mm would be ideal for this. To calculate the minimum screw length, the screw-in depth must be added to the attachment thickness. This can be determined in a simplified way from the dowel length and the diameter of the screw.
Screw length (in mm) = (dowel length (in mm) + Ø screw (in mm)) + thickness of attachment (in mm)
In our example, we now fill the formula with the given values for the dowel length, the screw diameter and the material thickness to calculate the minimum length of the screw in millimetres.
Screw length (in mm) = (40mm + 4,5mm) + 3mm -> (44,5mm + 3mm -> 47,5mm
Screws with a length of 47.5mm are likely to be difficult to obtain. Screws in the size 4.5x50mm are therefore perfect for fixing the lightweight plastic panel to the wall with dowels.
NOTE:For our screws, we have listed the minimum anchoring depth in the additional information.
The screw head is sometimes of great importance during assembly. Countersunk screws are the ideal choice, especially for the assembly of wood materials and plastic, where the screw connection should be flush with the surface of the assembly part. On the other hand, screws with a half-round head are more suitable for a firm tightening torque of the object to be mounted with the substrate. This applies both to the direct screwing of materials together and to assembly with screws and dowels.
When using dowels, the placement of the dowel must also be taken into account. For push-in installation, both a countersunk screw and a half-round screw can be used. The only thing to consider here is whether the screw head is to be countersunk or whether surface mounting is desired. If the assembly part is fastened in the push-through assembly, in which dowels are inserted through the material into the substrate, a half-round head is always the better choice.
Screws with countersunk heads are used when flush mounting with the surface is required. For wood materials, the screw is screwed into the material until the head is flush with the surface. Pre-drilling the countersink is not necessary for softer softwoods. With hard types of wood, such as walnut or oak, as well as with metals and plastics, however, the surface must be machined in advance with a countersink. Otherwise, the screw cannot be fully countersunk into the hard materials. If the torque acting on the screw is too high, this can even cause the screw head to break off.
Countersunk screws are used in the trade for flat cladding with chipboard, in dry construction for erecting walls made of plasterboard or also for screwing substructures made of wood that are later to be clad with panels.
Screws with a half-round head are lenticular to round on the upper side, whereas the lower side offers a smooth contact surface to the screw shaft. Such screws, the head shape of which is often also referred to as PAN head, cause a high tightening torque of the assembly part on the assembly base or the substructure due to the smooth contact surface. Due to the head geometry, the screw head protrudes and is not flush with the material.
The use of washers increases the contact surface of the screw head, which prevents it from sinking into softer materials. In addition, this causes an optimised distribution of the tightening torque on the assembly part. A typical example of screws with lenticular half-round heads are our facade screws or balcony screws with metric thread, where the screw is tightened until the head rests on the plate.
Screws with a classic lenticular head combine the two head shapes, so that the top is lenticularly rounded, while the bottom has a countersunk head shape. These screws can be countersunk to a certain extent in the material of the assembly part, whereas the upper head area protrudes with the drive. The rounded shape prevents injuries. Pan head screws are used, among other things, when laying decking boards made of wood or WPC (wood-polymer compound).
The thread type of a screw depends on the material in which the screw is to be screwed in. A distinction is made here between two important main groups. The coarse thread and the fine thread.
For mounting in wooden beams or of wooden boards, screws with coarse threads are usually used. These are available with a partial thread or full thread. The advantage of a partial thread is that the components can be pulled together without a gap, as long as the threadless shank is at least as thick as the attached part. A fully threaded screw, on the other hand, distributes the load over the entire length of the screw, allowing higher tensile forces. Typical examples of screws with coarse threads are dowel screws, which screw into the dowel quickly and easily and ensure that the dowel functions properly. Our facade screws with partial thread also belong to the screws with coarse thread and are used for mounting HPL panels in wooden substructures. The shank ensures that the panels are mounted without any constraints.
Screws with metric fine threads, on the other hand, are mostly used for mounting on or of metals. Here, the thread is either cut directly into the metal and the screw is screwed in, or it is mounted on both sides by means of a hexagon nut or cap nut, as is the case with our balcony screws for erecting balcony surrounds on balcony railings. Wall or ceiling mounting of threaded screws with conventional dowels, on the other hand, is not possible. Special dowels with internal threads in the appropriate size are required for this. An example of this is the installation of cold clamps or threaded rods.
There are other thread variations, such as the double thread, the inch thread or also the internal thread, which are, however, rather required for special applications.
The drive of a screw not only defines which tool is needed for assembly, but also provides information about the way it can be assembled. Hexagon socket screws, which are known to most as Allen screws, as well as screws with an external hexagon, allow sideways assembly, which means that they can also be used in narrow, hard-to-reach areas. Screws with slot, cross recess or also hexagon socket (e.g. TORX screws) are usually screwed in frontally with a screwdriver or screwdriver bit.
In addition, the different drives also allow different levels of tightening torque, which can be achieved with more or less effort depending on the type of screw drive. A simple slotted head screw achieves only a very low tightening torque despite a high effort, while hexagon socket or external hexagon can be tightened very strongly without requiring a great deal of effort. Our countersunk screws of the PowerFast II series from fischer have a hexagon socket drive whose high tightening torque enables flush screwing with the mounting part. With most wood-based materials or plastics, there is no need to countersink with a taper countersink beforehand.
The most common drives include the simple longitudinal slot, the cross slot, as well as its further developments Phillips and Pozidriv, the hexagon socket (also known under the brand name TORX), the hexagon socket (common under the brand name Allen) and the external hexagon.
Most screws used in households and by craftsmen and industry are made of steel or stainless steel. Aluminium and brass are also popular alloys for making screws. Plastics are also used for screw connections, but due to low loads, they are less common. Regardless of the material from which a screw is made, it is always a valuable raw material that can be recovered through recycling or melting.
Screws made of plastic can be disposed of very easily by recycling them in the yellow bin. Unfortunately, there is no separate bin for metals, so they usually end up in household waste. Unfortunately, this means that the raw materials are lost. For a sustainable recycling cycle, it would make sense to take screw material that is no longer needed to a local metal processor or to a scrap dealer, who, at least in our region, drive through the streets almost every month. For very large quantities, you may even be able to get a few euros from a recycling company. Individual screws, on the other hand, are not paid for.