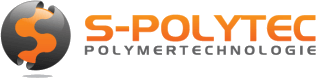
For particularly heavy loadsyou have to use particularly robust fasteners. With ourhigh quality heavy duty anchorsa secure hold is guaranteed for the long term.
Incl. 19% Tax
Incl. 19% Tax
Incl. 19% Tax
Heavy-duty anchors are always used when installation with conventional dowels and screws cannot guarantee the mechanical anchoring of heavy or particularly stressed loads. Depending on the mounting surface, one or more fastening solutions are possible, some of which differ significantly. However, these heavy-duty fastenings have one thing in common - they can withstand enormous loads. To ensure that they are held permanently and securely, it is crucial to precisely determine the building material of the substrate as well as its condition. Furthermore, precise drilling and compliance with the specified tightening torques are very important.
Our range of heavy-duty fasteners is as varied as the mounting parts and the loads acting on the mounting surface. Our range not only includes different designs, but also variations in diameter, length and usable length.
Once firm is firm - so why buy too many anchors?
With our heavy-duty fasteners, we offer the right mounting material for heavy loads so that a secure hold is guaranteed when it counts. It doesn't matter whether you need 8 bolt anchors to fasten the garden swing for your children or 25 boxes are needed to mount the railings in the staircases of a new housing estate. We offer you the heavy-duty anchors in a great many designs and types, regardless of quantity or cumbersome packaging units - starting at one piece.
NOTE:Other sizes, as well as mechanical anchors for special applications, are available at short notice on request.
Bolt anchors made of steel are the perfect choice for securely anchoring heavy loads that do not come loose at any time, even under heavy mechanical stress. For this reason, bolt anchors are used for the installation of fall protection, such as stair railings or balcony railings. In addition, bolt anchors are used to securely fasten playground equipment, such as a climbing frame, a swing or a water slide. The enormous loads that this fastening must hold must also be able to be held by the substrate, which is why bolt anchors are almost exclusively approved for use in concrete.
Wedge anchors are usually made of steel, as this has very enormous strength classes. A distinction is made between different qualities in terms of the alloy and the possible areas of application. Not every bolt anchor is suitable for outdoor use, so when selecting our range, we deliberately chose a steel anchor from Fischer that is made of stainless steel so that our substructure profiles for cladding exposed concrete walls can also be fastened outdoors with it.
NOTE:For detailed information on available approvals, as well as application possibilities and restrictions, please refer to the respective product description.
There are three main types of heavy-duty anchors, which are more or less suitable for different fastenings. It is not only important to consider the material in which the heavy-duty anchors are to be fastened, but also very important where exactly they have to be installed. What is to be fastened with a heavy-duty anchor and how long the fastening has to remain in use determines which anchor type is well suited and which technique is at a disadvantage here.
The best-known heavy-duty anchor is the bolt anchor, which is often also called a steel anchor or impact anchor. This is usually made entirely of steel. A plastic anchor is not required for installation. The advantage of the bolt anchor is the reliability of the fastening, even if it is subject to heavy movement, because steel is unyielding, unlike a plastic anchor. The downside of a steel anchor inserted into concrete is that it can only be removed again with great effort. Bolt anchors owe their name to the conical bolt which, when the nut is tightened on the opposite side, causes the steel expansion clip to expand. This is spread so far that there is no more play between the metal sleeve and the edge of the drill hole.
Concrete screws are screwed directly into the concrete without an additional dowel. It is very important to use a suitable drill bit because the thread of the concrete screw must cut into the concrete. If the drill diameter is chosen too large, the thread will not have sufficient hold in the concrete. The advantage of concrete screws compared to bolt anchors is that they can be easily removed and also do not exert high pressure on the drill hole.
Composite anchors are also among the widespread heavy-duty fixings where the anchor is fixed in the drill hole with a special adhesive or injection mortar. By gluing the anchor, no stresses are created in the drill hole that could lead to cracks. Thus, an injection anchor - as this type of heavy-duty anchor is also called - is excellently suited for fixing close to the edge in concrete or also solid and hollow bricks. The disadvantage, however, is that the anchor cannot be loaded immediately and the hardening of the injection compound must be waited for.
When it comes to the material, you have to look twice, because you have to distinguish between the building material and the material of the anchor. Not every heavy-duty anchor can be used with every installation substrate. Bolt anchors have such enormous force that the expansion clip can burst the drill hole if the building material is not strong enough or if the anchor is placed too close to the edge. This is why they usually only have ETA approval when used in concrete. Although the hold is also very good with solid stone, a tested approval is not available for the combination in most cases. There are also differences in individual bolt anchors, which, depending on the design, material and manufacturer, are only suitable for cracked or non-cracked or both static loads. Whether a heavy-duty anchor is only suitable for indoor use or whether it is made of stainless steel and is also suitable for outdoor use should also be checked before purchasing.
In order to securely fasten heavy loads, it is very important to deal with the substrate. It should be clear what material is involved and what structural loads act on the mounting substrate. A distinction is made between tensile stresses (for example, a concrete ceiling) or compressive stresses, for example, a wall made of exposed concrete. If the installation takes place in an area where the tensile stress is quite high, bolt anchors for cracked concrete should be used. If, from a static point of view, there is a high pressure on the assembly area, we are talking about non-cracked concrete, so the corresponding steel anchor must also be used here.
NOTE:Which heavy-duty anchors have an ETA approval and for which building materials these approvals apply can be found in the respective product description.
The size of the heavy-duty anchor can certainly play an important role. The theoretical load capacity can be calculated with the diameter of the anchor. The larger the diameter, the higher the load on the anchor. However, it does not make sense to always use the largest heavy-duty anchors, because the load must ultimately also be able to be carried by the installation substrate.
The length of the anchor is doubly important. The anchoring depth is important because this value indicates how deep the heavy-duty anchor must be inserted into the drilled hole. This specification should not be confused with the total length of the anchor. With increasing anchoring depth, the anchor has more hold in the installation substrate and thus the theoretical load capacity is also higher. The effective length indicates how high the thickness of the mounting part may be so that the nut or cap nut can still be screwed onto the thread and tightened with sufficient torque. A useful length of 10mm means, for example, that the mounting plate of the railing must not be thicker than 10mm.
NOTE:The required anchoring depth must never be undercut. The effective length should also always be sufficiently large.
Heavy-duty anchors are used when the load on the fastening is so high that conventional screws and anchors are no longer sufficient. Plastic anchors quickly reach their limits, especially when the fastening is subjected to impact or movement. With so-called dynamic loads, heavy-duty anchors are often the only method to achieve a permanently secure fastening.
Heavy-duty anchors are used, for example, to fasten playground equipment and climbing facilities. Regardless of the weight, heavy-duty anchors are also used when the fastening of objects classified as safety-critical is required. These include fall protection such as stair railings, as well as steel railings of balconies and roof terraces. The installation objects themselves are also classified as safety-critical if they pose a danger to persons or high material damage due to loosening of the fastening or falling down.
In den meisten Fällen, genügt es jedoch nicht, eine Montage mit einem Bolzenanker, einer Betonschraube oder einem Injektionsdübel zu befestigen. Für die Montage von Lasten gelten unterschiedliche Normen. Eine durchdachte Planung und präzise Ausführung von Schwerlastmontagen, ist ebenso wichtig, wie das geeignete Befestigungsmaterial selbst. Da wundert es nicht, dass auch das Montagematerial über eine entsprechende Zulassung für den konkreten Montagezweck vorliegen. Bei der Montage mit Schwerlastankern ist daher die ETA-Zulassung verpflichtend. Diese regelt, in welchen Werkstoffen ein Anker verwendet werden darf, wie diese montiert werden müssen und gibt Aufschluss über die Belastbarkeit, bei fachgerecht ausgeführter Montage.
NOTE:Our heavy-duty anchors all have ETA approval. These can be viewed and downloaded on the respective product page in the Downloads section.
Wedge anchors can be loaded immediately after installation. To use a steel bolt anchor as a fastening, the first step is to drill the hole. The drill diameter should correspond to the diameter of the bolt anchor. When drilling, it is important to drill straight and deep enough. If the hole is drilled too crooked, the nut cannot be tightened properly and the tightening torque will only be applied to part of the nut. The depth of the hole varies depending on the length of the anchor.
Depth of hole = anchorage depth (in mm) + 10mm
Due to the enormous force of the expansion clip acting on the edges of the drill hole, sufficient edge distance of the drill hole must be observed. If this distance is too small, the surface of the concrete can tear out, break or even flake off. In these cases, the heavy-duty anchor does not have sufficient hold and a safe installation is no longer guaranteed.
Min. edge distance (in mm) = Ø bolt anchor (in mm) * 6
This means that with a bolt anchor of type FAZ II in size 10/3, an edge distance of more than 60mm should be maintained and the hole must be at least 105mm deep according to the manufacturer's specifications. With a depth stop or a marking on the drill (e.g. coloured insulating tape), you can ensure that all holes are drilled sufficiently deep.
After drilling, there is still drill dust in the drill hole that was not removed from the hole by the drill spiral. This acts as a sliding layer, especially in the case of wall mounting, and reduces the frictional connection of the expanded metal sleeve to the edge of the drill hole. Sucking out or blowing out with compressed air is sufficient to free the borehole from the last of the drill dust.
The bolt anchor can then be inserted straight into the drill hole. To achieve the anchoring depth, light blows with a hammer are necessary. Be careful when doing this, because if you hit the nut, it can tilt or the thread can be damaged. Special setting tools that are adapted to the size of the nut make setting the bolts much easier and save a lot of time.
In the last step, the mounting part can be placed, if this has not already happened before drilling (usual when fixing heavy-duty shelves). To do this, the nut must be removed. This is then screwed back on and tightened until the necessary torque is reached. A torque spanner ensures that the tightening torque is reached.
A sharp drill bit should always be used when drilling. A PGM test mark ensures that the drill bit has been tested for roundness and quality, which can prove very important, especially when fastening with bolt anchors. Poorly drilled holes can mean that the tapered bolt does not expand the expansion clip or does not expand it sufficiently. A secure fastening of the attachment part can therefore possibly no longer be guaranteed.
Concrete screws have the advantage that they can be removed very easily, which is by far not the case for all heavy-duty fixings. Installation is also basically very simple, but here, too, care should be taken to drill a clean, straight hole. The depth of the hole is usually specified by the manufacturers. In most cases, it should be at least 10 mm deeper than the anchoring depth of the screw.
Depth of hole = thread length (in mm) - thickness of attachment (in mm) + 10mm
If a balcony railing whose mounting plate has a thickness of 12mm is to be fastened to a concrete beam with a concrete screw of size 8x100mm, this results in an anchoring depth of 88mm. Consequently, a minimum depth of 98mm must be drilled.
After drilling, the drill hole should be cleaned of drill dust by briefly blowing out or sucking out. This makes it easier to screw in the screw and, above all, deep enough. Screwing in concrete screws requires strength and, depending on the head shape and drive, the appropriate installation tool. Before a concrete screw is used, it is imperative to pay attention to the design of the screw head and drive. For steel girders or railings made of metal, a surface mounting of the screw head is necessary, for which a tangential impact spanner socket with the corresponding spanner size is usually used. Concrete screws with countersunk heads, most of which have a Torx drive, are only suitable for through-fixing on wooden mounting parts, or if the hole in the mounting part has previously been widened with a countersink so that the countersunk head can be flush.
As with drilling the holes for the bolt anchors, a tested drill should always be used for concrete bolts. Concrete screws should withstand great loads. In order to guarantee this and to prevent dangers for humans and animals due to falling or falling down, the drill should not be too worn in order to be able to drill a precise hole.
Composite anchors, in contrast to mechanical heavy-duty anchors, are not immediately loadable because an injection compound must harden before installation. Due to this chemical process, composite systems are also referred to as chemical heavy-duty anchors. Of course, holes must be drilled for chemical anchors that correspond in diameter and depth to the steel anchor that is to be used for the fastening.
After drilling, the holes must be cleaned thoroughly. An attachment with a cleaning brush in the diameter of the drill hole is recommended, because this loosens even fine dust residues at the edge of the drill hole, which can then simply be blown or vacuumed out. If cleaning is not carried out, the drill dust prevents the injection compound from coming into contact with the edge of the borehole. This considerably reduces the load-bearing capacity of the chemical anchorage and can cause the installation part to fall down. Only after cleaning can the injection mortar, the two-component adhesive, or the reaction cartridge be injected into the borehole. The insertion of the steel anchor should be done promptly, without much delay.
Depending on the injection compound, slight corrections can still be made to the steel anchor before the compound begins to harden. How long the complete hardening takes depends on the adhesive or mortar. It is imperative to follow the manufacturer's instructions so that the fastening is not stressed too early by the weight of the mounting part or the tensile load of the fastening nut.
Injection systems are highly recommended compared to heavy duty mechanical fixings when the fixings holes are close together. With bolt anchors, spreading could cause cracks or spalling to the wall corner or adjacent holes. This danger does not exist in the case of a tension-free material connection with bonded anchors. For the same reason, chemical heavy-duty fixings are also suitable for hollow bricks, although depending on the design and manufacturer, it is always necessary to check whether there is an ETA approval confirming that the specific bonded anchor may be used for the specific material of the installation substrate.
When setting bonded anchors with injection mortar or a special adhesive, it is imperative that sufficient curing takes place before the installation of the mounting part can begin.
Heavy-duty anchors cannot be removed as easily as a conventional fastening with screws and dowels. The exception here is concrete screws, which can simply be unscrewed again with the appropriate tool. Bolt anchors, on the other hand, can only be removed with effort and force. To do this, loosen the nut far enough so that the threaded rod can be driven into the drill hole with a hammer in the hope that the conical bolt will loosen and release the splayed metal sleeve. Finally, the bolt can be levered out of the drill hole with a crowbar. This requires a lot of force. In some cases it can be helpful to loosen the bolt a little by light lateral blows in several directions.
In the case of chemical anchors that have been fixed with steel anchors and injection mortar, in most cases only drilling out the anchor will help. The injection systems were developed to withstand the greatest loads, so that with mere leverage there is no real chance of pulling the bonded anchor out of the wall. Drilling out is also a possible variant for bolt anchors that cannot be removed by levering with a crowbar.
Most heavy-duty anchors are made of steel or stainless steel, because this material has enormous tensile strengths, which are required for heavy loads. Steel can be recycled excellently and almost as often as desired, regardless of whether it is simple galvanised steel or stainless steel. The screws, bolts and all other steel scrap are melted down at very high temperatures. The raw steel obtained in this way can be used in further processing to produce steel pipes, steel girders or new fastening techniques. For this reason, screws and bolt anchors should not be carelessly disposed of in the residual waste, but at a scrap dealer or recycling centre. Crafts enterprises that regularly produce scrap metal are also generally happy to accept old screws and bolts in order to feed them into the recycling circuit.
Unfortunately, heavily contaminated heavy-duty fasteners based on injection systems are usually not used for recycling because they have too much contamination adhering to them due to the assembly adhesive.