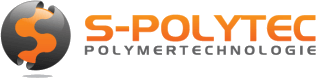
For the erection of facade claddings on an existing substructure made of aluminium, we offer you the matching facade rivets made of aluminium in various lengths. Optionally, even with a matching top coating to our HPL facade panels in RAL.
Incl. 19% Tax
Incl. 19% Tax
Incl. 19% Tax
Incl. 19% Tax
Incl. 19% Tax
Incl. 19% Tax
Incl. 19% Tax
Incl. 19% Tax
Incl. 19% Tax
As a specialist dealer for plastic panels, we offer a wide range of panels that are suitable for use as cladding panels. Some of these also have a facade approval, so that they can be used as cladding for facades in outdoor areas. In order to guarantee you maximum flexibility, we offer our plastic panels not only in millimetre-precise cut-to-size, but also carry the appropriate mounting material for the respective materials. This also includes our facade rivets, which, as large-head blind rivets, are ideally suited for the construction of facade claddings, balcony surrounds or privacy screens.
Unlike most online retailers, we do not offer our facade rivets in boxes with packaging units of 100 or 250 pieces. In our shop you can buy our rivets in your desired quantity - and that already from a single rivet. You also benefit from our generous quantity discounts, which are automatically taken into account depending on the quantity you order.
Facade rivets are extremely practical when a firm connection is to be achieved but assembly is only possible from one side. This is probably why blind rivets owe their name to the fact that the rivet is placed through the elements to be joined from the visible side, whereby the back is not visible or is concealed in such a way that it cannot be reached, for example to fix a lock nut. However, rivets are not suitable for mounting panels on wood, because wood is a very soft material that does not guarantee a secure hold even when the aluminium sleeve, which is the actual rivet, is squeezed together. When mounting facade panels on wooden profiles, facade screws with coarse thread should therefore always be used. These are also available in the online shop in various colours. Our aluminium rivets are also not suitable for substructures made of steel or stainless steel, as this can lead to contact corrosion due to the material mix, which can have a negative effect on the durability of the rivet joint.
IMPORTANT: The aluminium facade rivets are only suitable for existing aluminium substructures. Only use facade rivets made of a steel alloy for steel substructures.
Making a rivet joint with a blind rivet, which also includes our facade rivets, is particularly useful if the assembly can only be carried out from one side. In this case, the blind rivet is inserted into the drilled hole with the sleeve first until the head from which the mandrel protrudes rests on the plate to be assembled. Then the mandrel, which in our facade rivets is made of high-quality stainless steel, is inserted into a suitable nose piece of the riveting pliers. The mandrel has a thickening at the end of the sleeve, which squeezes the sleeve together when the blind riveter is actuated until the tightening torque is so great that the mandrel breaks at the predetermined breaking point and falls out of the hollow rivet sleeve. The biggest advantage of riveting facade panels is that a connection made by riveting is durable and secure. In contrast to screwed joints, there is no risk of the rivets coming loose over time due to impact or vibration. In addition, a blind rivet that has been set can be loaded immediately after it has been set.
Facade rivets are mainly used for the assembly of facade panels. For this purpose, HPL panels are often used, but also fibre cement panels or aluminium composite panels, for which a constraint-free installation is extremely important so that the facade panel can expand without any problems, without an installation with too high tightening torque counteracting the thermal expansion. The tightening torque of a fastening depends not only on the type of mounting material, but also on the material of the panel to be used for the facade cladding. The same applies to balcony surrounds or when erecting privacy fences that are to be erected with plastic panels for outdoor use. In the case of facade screws and balcony screws, the tightening torque is defined by the torque during screwing. However, this is not the case with blind rivets, so that, depending on the material, a special nose piece must be screwed into the riveter. These so-called special gauge mouthpieces are available for aluminium composite panels and HPL panels (and fibre cement panels) and guarantee a firmly defined gap distance between the panel and the rivet head.
We offer aluminium facade rivets either unpainted or with a scratch-resistant top coat in different sizes. Even if the lacquering is matched to our HPL panels in RAL colour, the rivets can also be used excellently for a variety of other plastic panels from our online shop. Especially for the black and white rivets, almost all of our panels in black or white are suitable for attaching them as unobtrusively as possible. You are not limited to the construction of facade claddings, even if the term facade rivet suggests it. As blind rivets, our facade rivets can also be used without hesitation for riveting plastic housing parts with aluminium angles or for mounting decorative strips in visible areas.
TIP: Depending on the cladding material, a special gauge mouthpiece is required for a constraint-free installation of facade panels with our facade rivets.
We stock facade rivets not only in different colours with scratch-resistant head lacquer, but also in different lengths, each with a different clamping range. This depends on the thickness of the plastic panels and the thickness of the substructure. Starting from a typical thickness of 2mm for the aluminium substructure, a facade blind rivet in the size 5x14mm is most suitable for our aluminium composite panels with a thickness of 3mm, or aluminium composite panels with facade approval in 4mm thickness. If instead HPL panels are mounted on the same substructure, our facade rivets in the size 5x16mm are the ideal choice for panels with a thickness of 6mm, and for HPL panels with a thickness of 8mm we recommend the rivets in 5x18mm.
Facade rivets are usually used for existing substructures made of aluminium profiles, where the fastening is done on one side. Mounting with fixed and sliding points is the normal case. While the substructure is always drilled in the same size when riveting, the cladding panels are drilled with different diameters. For our facade rivets we recommend our ground HSS drill with 5.1mm diameter for drilling the fixing points in the load-bearing aluminium profiles. For the fixing points, the drill should also be selected in the size matching the rivet. For the sliding points, a larger diameter of 8mm or, in case of high thermal expansion, a 10mm drill is advisable so that the temperature-related expansion of the panels can be absorbed without stress. Whether an HSS drill should be used, or better a drill made of solid carbide, depends on the type of cladding material.
In order to make rivet joints with our facade rivets, a blind riveter is required. Depending on the extent of the rivets to be set, a cordless riveting tool or a riveting tool with compressed air can make the work much easier. However, these special riveting tools are very expensive, so that they only pay for themselves when used regularly or with many rivets. For occasional riveting, a commercially available blind riveter is also sufficient. If the rivets are used for the installation of cladding panels in the case of facade cladding or balcony surrounds, it is urgently necessary to check in advance whether a constraint-free installation is necessary. Especially with HPL panels, fibre cement panels and also aluminium composite panels, the thermal expansion contributes to the fact that for the assembly with our facade rivets a special special gauge mouthpiece is required, which is screwed into the riveter. Here we differentiate between aluminium composite panels and HPL panels, as these require different tightening torques when riveting. For claddings with aluminium composite panels, the special ALU-16 gauge mouthpiece is the right choice, which is suitable for facade rivets with a diameter of 16 mm. However, this special gauge mouthpiece cannot be used for HPL panels. This mouthpiece is also only suitable for facade rivets with 16mm head diameter and can be used for the assembly of HPL panels as well as fibre cement panels.
TIP: When drilling the panel, make sure that it is on a firm surface to avoid chipping when the drill bit exits. For drilling HPL panels, we recommend using an 8mm diameter solid carbide facade panel drill bit.
How many rivets are required cannot be answered in a generalised way, because the intended use, as well as the cladding material used, can contribute to the fact that the required number of fastening points can vary considerably. Even with the same material, a different number may be required, even if the dimensions of the panel differ only slightly. It is therefore advisable in any case to check in advance how the corresponding plastic panel is to be installed and whether legal regulations may apply.
Regardless of the intended use of our facade rivets, it must be checked in advance whether a European standard or a DIN standard is specified for the respective assembly. These must be complied with in any case, so that the required number of fixing points must never be below the valid standards and guidelines. Especially when erecting facade claddings and balcony surrounds, it is extremely important that the installation is carried out in accordance with the valid guidelines, as otherwise it can lead to problems during the acceptance of the building project. If the installation is carried out by a specialised company, they usually know which laws, standards and guidelines must be observed for the project in question.
If you want to cover your balcony railing to achieve effective privacy protection or to prevent it from falling off the balcony, this can be done with facade rivets. However, it is important that the balcony cladding is constructed with plastic panels that comply with the ETB directive. Furthermore, aluminium facade rivets can only be used if the balcony railing is also made of aluminium. Otherwise, contact corrosion may occur due to contact between different metal alloys. As a rule, balcony balustrades have the necessary number of fixing points, so that the number for fixing can be adopted.
The required number of fixings can vary not only for balcony surrounds, but also for the flat cladding of facades. It is therefore advisable to consult the installation instructions for the plastic sheeting used. The instructions often also provide information as to whether a constraint-free installation with fixed and sliding points must be carried out and which installation material may be used in principle.
In some cases, it may be necessary to increase the number of fixing points, as this contributes to a more pleasing visual result. This can be the case, for example, with narrow, long plastic panels, where the distances are taken over on the narrow side in order to achieve the same distances on the long side by means of more rivet joints. However, it is not possible to increase the distance between two fixing points in such a way that the installation can no longer be carried out in accordance with the installation instructions or the applicable standards.
Depending on the format of the panels, even with identical surfaces that need to be clad, there may be significant variations in the quantity of facade rivets required. A panel with a format of two metres in length and one metre in width, as a whole panel, is usually sufficiently fastened with 12 facade rivets, if a fastening distance of about 50 centimetres is taken as a basis. If the identical surface is covered with two panels in a square format of one metre by one metre, then eight facade rivets are already required for each panel, making a total of 16 rivets. Assuming that the same area is covered with 4 panels, each of which has a format of one metre in length and half a metre in width, the required quantity increases again. In this example, 24 rivets are required for fixing, without the distance between the mounting points of a single panel differing significantly from the 50cm in the first example.
TIP: Depending on the panel thickness and also the material thickness of the aluminium profiles used, facade rivets in different sizes with different clamping ranges may be required.
Our facade rivets are made of a high-quality aluminium alloy with a stainless steel rivet mandrel. This combination guarantees a permanent, secure hold of the facade panels and has a very good resistance to weathering. Even the scratch-resistant head coating is UV-resistant, so that the rivets hardly require any special care after installation. In case the facade claddings need to be cleaned, this can easily be done with conventional cleaning agents and water. However, do not use microfibre cloths or scouring agents, as this can not only affect the surfaces of the assembled panels, but also damage the painted surfaces if the pressure is too high. With a simple sponge or a soft cloth, cleaning the cladding panels and the rivet heads is usually very easy.
Our facade rivets consist of two main parts, but they are made of different materials. The rivet mandrel is made of stainless steel and is separated at the predetermined breaking point after a rivet joint has been made, leaving only the drawn-together rivet sleeve and the rivet head made of aluminium. If existing rivets are to be loosened, this can be done by careful drilling. The aluminium rivet head can be collected separately and disposed of at a scrap dealer or recycling centre. Individual rivets, on the other hand, can be disposed of with the residual waste, which, however, entails an unnecessary loss of valuable raw materials.