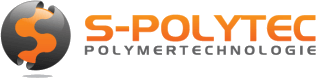
Plastic sheets are indispensable in the food industry because they are versatile and easy to process. The purpose for which a food-safe plastic sheet can be used depends on the properties of the sheet.
Incl. 19% Tax
Incl. 19% Tax
Incl. 19% Tax
Incl. 19% Tax
Incl. 19% Tax
Incl. 19% Tax
Incl. 19% Tax
Incl. 19% Tax
Incl. 19% Tax
Incl. 19% Tax
Incl. 19% Tax
Incl. 19% Tax
There is a whole range of plastics that are designated as food safe and are approved for contact with food. However, when which plastic can be used depends not only on food conformity, but also on other requirements for the properties of a plastic sheet. Some applications require a high degree of transparency, while others may require very high temperatures which the plastic must be able to withstand. Thermal formability for the production of finished plastic parts using the thermoforming process can also play an important role in the choice of a suitable plastic.
We at S-Polytec offer you an extremely comprehensive range of the most common plastics with approval for the food and drinking water industry. From the extremely inexpensive mass plastic polyethylene, to the harder polypropylene, to the glass substitute PETG. You also do not have to do without food-safe high-performance plastics such as PTFE (better known as Teflon®).
You benefit from our free cutting service, which cuts your plastic sheets to the exact millimetre to the size you require. Thanks to extensive stocks of our standard delivery programme, not only are very short delivery times guaranteed. You also profit from very favourable prices, because we are able to purchase our plastics at very favourable prices due to the large quantities purchased from our suppliers.
Plastics are very often used for the production of food contact materials or for food packaging. Plastics are inexpensive and, compared with most other materials, are extremely easy to process. In addition, plastics can be easily reprocessed by recycling and can be reused almost as often as desired.
Which plastic is used for which purpose always depends on the specific requirements of the plastic. Often, several suitable plastics can be considered for one and the same application.
Note: Please note that delivery times and shipping costs may vary for our extended delivery programme. Our sales staff will be happy to provide you with comprehensive advice on all questions concerning the use of plastic sheets in the handling of food.
In simple terms, plastic food contact materials and articles are all materials and articles made of plastic that are used for direct contact with food. This includes multi-layer materials and articles made of plastic which are held together by gluing, welding, screwing or any other means. Plastic layers or plastic coatings used for example as seals in caps and closures, or coatings composed of two or more layers of different materials are also plastic food contact materials and articles, provided that the plastic coatings are intended to come into contact with food.
In short. If it is an object made wholly or partly of plastic and intended to come into contact with food, it is always also a food contact material or article for which food conformity must be guaranteed.
In order for a plastic to be approved for the manufacture of food contact materials and articles and thus for contact with food, confirmation is required that this material complies with the relevant legal requirements and that the conditions for placing it on the market are fulfilled. In Europe these are classified by the declaration of conformity for food contact materials and articles made of plastic according to the EU regulation No. 10/2011 (and various others). Other standards and classifications that provide information about the usability of a plastic in the food sector are e.g. the Food and Drug Administration (FDA) of the United States or the guidelines of the German Food, Commodities and Feed Code (LFGB).
This chain extends from the requirements of the raw materials and processes used in plastics production, through the manufacturing process as such, to the finished product. For example, a food contact material or article may not be glued to other objects if either the glue is not food compliant or the other object does not meet these requirements. Otherwise the material or article is also no longer classified as food safe. The same applies to refinement processes of a plastic by coating, painting, laminating or the like. The declaration of conformity is intended to document compliance with the relevant regulations to the subsequent processor or user of a specific material in the value chain, as well as to the control and supervisory authorities. These guidelines and standards provide information on how a plastic must be designed before, during and after processing to make it suitable for contact with food.
When to comply with which standard depends on the country of destination where the food contact materials and articles are to be used. For Germany as an EU member state, compliance with the EU standards applies in principle. However, if the plastic parts are to be exported abroad, for example to the USA, the respective country-specific requirements must be observed and fulfilled. In our example, a food approval according to FDA would then be required.
Polyethylene is one of the most widely used plastics, not only in the food industry. However, a distinction must be made here between low-density polyethylene (LDPE) and high-density polyethylene (HDPE). LDPE is mostly used in the form of films for packaging meat and sausage products. Plastic carrier bags, such as those used in the retail trade or at weekly markets, are also made of low density polyethylene (LDPE). Retainer films or viewing windows in food packaging, which are mostly made of paper or cardboard, are also often made of LDPE.
High density polyethylene, on the other hand, is more stable and impact resistant and is therefore very often used for plastic bottles. This does not refer to the well-known one-way and returnable deposit bottles, but to packaging for barbecue sauces, ketchup, mayonnaise and the like. Because HDPE has a very good resistance to chemicals and can also be used at temperatures of -50°C to +80°C, this plastic is also used for food storage, for example, as a fresh food can. Food can be stored in the freezer or heated in the microwave. Other examples of food contact materials made of HDPE are fresh water tanks in motorhomes, caravans or caravans, raw material containers in the food industry, or even worktops, cutting boards and cutting boards, whereby the latter are often also made of the harder polypropylene due to the lower surface hardness of polyethylene. Polyethylene sheets are also very often used for machine components, covers and conveying elements that are in direct contact with food before, during and after processing in food production.
The two plastics, i.e. LDPE and HDPE, can be easily distinguished by the recycling code on the food contact material. The recycling code for HDPE has the sequence of digits 02, whereas the digits 04 identify a plastic product made of low density polyethylene.
Polyethylene terephthalate is probably one of the most common plastics used in food and drinking water processing. Hardly any major beverage producer does without the use of returnable PET plastic bottles. This is not only considerably lighter than glass, but also extremely robust, very easy to recycle and very easy to shape by injection moulding. However, PETG is not only used for returnable bottles. Because of its complete colourlessness and high light transmission, plastic sheets in refrigerators and refrigerated counters are often made from the frost-resistant PETG sheet.
Another advantage of the transparent plastic with food approval is its fire behaviour, as PETG is classified as flame-retardant according to DIN 4102 B1.
Polypropylene is the low-cost all-rounder among the food-conforming plastics and is used for almost all purposes where a higher surface hardness than polyethylene is required. Especially for cutting pads and breakfast boards or plastic tableware for camping use, PP is very often used for production. This plastic is suitable for microwave ovens, dishwasher safe and can also be used for fresh food cans or storage containers for freezers, as the temperature range of polypropylene is from -40°C to +110°C. In the short term, heat resistance up to +140°C is even possible. As packaging for food, PP is used for yoghurt cups or margarine, among other things.
PTFE is a high performance plastic and is more commonly known under the brand name Teflon®. However, this plastic is not only used for coating pots and pans, but is characterised by a whole range of positive properties. First and foremost, PTFE is a plastic with an enormous temperature application range of -200°C to +260°C. PTFE is indispensable, especially in the industrial processing of foodstuffs, where extremely low temperatures are required for rapid cooling of raw materials and products. But PTFE is also a very suitable plastic material for high temperatures where food is pre-cooked by baking, steaming or boiling.
Furthermore, PTFE is characterised by its enormous chemical resistance. This plastic is chemically inert to such an extent that it does not react with any foodstuff and thus does not adhere to the plastic surface. This results in extremely easy cleaning. The best example is once again pots and pans with non-stick coatings made of Teflon®. This aspect is also taken into account when choosing a suitable plastic for machines and systems that process and produce food, because cleaning and maintenance of production lines should be carried out quickly and without great effort, in order to ensure the greatest possible efficiency in the production of food.
Another noteworthy property is the very good sliding behaviour of PTFE - even at the most adverse temperatures. Outside of food contact, this plastic is used for sliding bearings of bridges, among other things. In food production, the very good sliding properties are primarily used in food conveying technology.
Finally, it should be mentioned that PTFE meets the very strict requirements of the UL94 V0 fire protection standard. This plastic is therefore considered non-flammable.