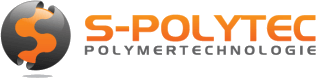
Our crystal clear and weather resistant acrylic sheets (also known as PMMA) are no multi-wall panels, but solid smooth sheets covered both sides with a protective film. We can supply you with custom cut sheets at affordable prices.
Incl. 19% Tax
Incl. 19% Tax
Incl. 19% Tax
Incl. 19% Tax
Incl. 19% Tax
Incl. 19% Tax
Incl. 19% Tax
Incl. 19% Tax
Incl. 19% Tax
The easiest way to buy acrylic sheets online is to use our cut-to-size configurator. Benefit from our low prices, a simple order process, perfect cuts exactly to your specifications and fast delivery. The processing - i.e. the cutting of your order - usually takes place on the next working day.
Buying acrylic glass blanks is child's play thanks to S-Polytec's blank configurator. Simply select the desired thickness of your acrylic sheet and enter the required dimensions for length and width in millimetres (not centimetres). The price calculation takes place immediately after your input and automatically takes quantity discounts into account, so that you always get the best price for you depending on the total weight.
Thanks to high material stocks for our standard delivery programme and fully automated work processes, we are able to offer you particularly favourable prices for your customised acrylic plastic sheets. The cutting is done on one of our computer-controlled panel saws for horizontal cutting with a very low sawing tolerance of only +/-1mm. You only pay for what you order. Thanks to a complex cutting optimisation and storage system, leftovers are used for further cuts and are therefore not charged to you. This also has an effect on the favourable price for our cut acrylic sheets.
Note: Please note that the delivery times and shipping costs for our extended delivery programme may vary. Our friendly advisory staff will be happy to answer any questions you may have about our acrylic sheets.
The configuration of individual laser parts made of acrylic glass with our laser part configurator is just as easy as our conventional acrylic glass cuts. The most common basic shapes are available to you as a pre-selection, which you can further adapt according to your needs. Even hole drillings can be placed in no time at all with just a few mouse clicks.
Even more individual? Laser parts according to your drawing or laser engravings are also possible on request. We will be happy to advise you comprehensively on the possibilities we can offer you with our laser service. Simply give us a call or send us an e-mail with your enquiry.
Do you want individual shapes made of acrylic glass that are not possible with our laser part configurator because either you need larger dimensions or higher thicknesses? With our milling service, this is no problem at all. With our modern milling centres we are able to produce milled parts up to a maximum format of 4000mm x 2000mm. And that even up to a thickness of 140mm. In addition, with our 3-axis milling machines we are also able to carry out recessing, countersinking or relief milling. Chamfering (i.e. rounding or bevelling) of cut edges is also possible with our milling service.
Due to the large number of possibilities, our milling service is currently only available on request. Simply send us your requirements with a design drawing and tell us the desired number, as well as the thickness and design of the acrylic glass sheets. Our experienced sales staff will contact you as soon as possible to provide you with a customised offer free of charge.
Acrylic glass blanks that are ordered via our online shop are usually cut to your ordered dimensions and shipped on the next working day. Depending on the dimensions and total weight of your order, delivery is either by parcel service or by freight forwarder on a pallet. You can see what your panels will be shipped with in the shopping cart. As soon as your order has been prepared for shipment, you will receive an e-mail with a tracking number.
Before packing, all acrylic glass blanks and laser parts are checked for quality of the cutting edge and dimensional accuracy. Afterwards, your order is wrapped in recyclable bubble wrap to protect it from delivery damage, and packed and shipped in outer packaging made of sturdy cardboard made of recycled paper. Please dispose of the bubble wrap and the strapping tape in the recycling bag or bin. Please dispose of the cardboard in your paper bin so that it can be recycled again.
Note: Acrylic glass cut to size or as standard sheets are always supplied with a protective film on both sides to protect the surfaces. However, this can be easily removed after processing.
Acrylic glass is an extremely versatile plastic. Thanks to its UV and weather resistance, it can be used for both indoor and outdoor applications. The plastic sheets are considered waterproof and do not rot when in contact with water, even when used permanently in contact with water (or under water).
In the building trade, acrylic glass is mainly used as balcony edging or as a translucent screen for balcony partitions. In window construction, the light, scratch-resistant plastic is not infrequently used for patio roofing. In gardening and landscaping, acrylic glass sheets are particularly popular as plastic glazing for greenhouses or garden sheds.
Acrylic glass has become indispensable in the automotive industry, and PMMA can be found in almost every vehicle. Be it as a glass pane for the instrument cluster, as a pane for the touch panel in modern cars. Headlight housings as deep-drawn parts, rear lights, indicator lights or plastic panes in lightweight construction (e.g. on some hard tops of convertibles) are partly made of acrylic glass. On caravans or motor homes, almost all windows and roof hatches (often called HeKis) are even made of double-glazed acrylic glass.
The advertising industry also likes to take advantage of the simple processing. As small advertising displays for new products, brochures, flyers and business cards, as advertising signs with printing or engraving, as illuminated displays or even large illuminated letters on company buildings. Even for the effective effect of indirect lighting within shops and shops, acrylic glass is used sensibly by the advertising industry.
Acrylic glass is a plastic that is characterised by very high transparency and very good light transmission. Furthermore, acrylic glass is a waterproof and weatherproof plastic that is suitable for indoor and outdoor applications. It is therefore often used as a transparent plastic pane to replace glass. Acrylic glass is UV-resistant in its natural form and thus has the advantage that even permanent UV radiation does not cause the plastic to fade, yellow or become brittle. In addition, up to 98% of UV radiation is blocked by the acrylic glass, so that the ultraviolet radiation does not penetrate the plastic pane. This is an extremely relevant plus point for patio roof glazing, as it also protects the patio furniture underneath from the effects of UV rays.
Acrylic glass, whose chemical name is polymethyl methacrylate, is often also referred to by the chemical abbreviation PMMA. This plastic is obtained by polymerising sulphuric acid, hydrocyanic acid, methanol and acetone. Each of these components is harmful to health on its own, but the polymerisation process produces a crystal-clear, transparent plastic that is above all harmless to health and is mainly used as a synthetically produced glass substitute.
The development of acrylic glass dates back to the first half of the last century. This plastic has existed since 1928 and was developed, among others, by the German company Röhm GmbH, which still sells acrylic glass under the brand name Plexiglas®. For this reason, the term Plexiglas is often used in the media and in normal language when acrylic glass is mentioned. Similar to handkerchiefs, however, there are many other trade names of different manufacturers under which acrylic glass is offered on the market. Brand names such as Acriglas®, Altuglas®, Apex®, Deglas®, Perspex® Plexiglas®, Senocryl®, Tecacryl® are all synonymous with the plastic polymethyl methacrylate and thus have the typical properties of acrylic glass, which differ only slightly depending on the manufacturer.
Acrylic glass is highly transparent in its natural form and emits light better than conventional glass. The light transmission of transparent acrylic glass is an incredible 92%. That of real glass is only between 85% and 90%, depending on the thickness of the glass plate. The biggest advantage in a direct comparison, however, is the weight saving, because acrylic glass weighs only about half with the same dimensions and the same thickness. This makes it an ideal and cost-effective substitute, especially for glazing where the statics do not permit a high weight.
As a genuine glass substitute, outdoor use is mandatory. Thanks to its UV and weather resistance, acrylic glass easily meets these requirements. The temperature ranges of acrylic glass do not limit this plastic for outdoor use. It is frost-resistant and can be used at low temperatures of up to -40°C. Even permanent temperatures of up to +40°C are possible. Even permanent temperatures of up to +80°C are no problem for acrylic glass sheets.
Thanks to their high surface hardness, acrylic glass sheets are particularly resistant to scratching, unlike most other plastics. Special surface coatings can increase the scratch resistance even further. However, such an additional surface finish can have a negative effect on the bondability with solvent-based adhesives because they cannot penetrate the coating to dissolve the plastic for effective bonding.
Another plus point is the thermal formability. Acrylic glass is a thermoplastic and as such can be easily moulded into almost any shape using the thermoforming process. With real glass, this is only possible at very high temperatures and in complex work steps, which not least affects the costs of production.
Acrylic glass can be cut in many ways. The easiest way to cut is with a saw and a saw blade with medium toothing at medium speed, as is done on our panel saws for our acrylic sheets made to measure. For straight cuts, a hand-held circular saw with a fence or a table saw is most suitable. Radii and curved cuts are better done with a handy jigsaw.
For routing with a CNC router, a simple router bit for metalworking can be used. Here, too, the speed should not be set too high to prevent the removed chip from fusing with the cut edge. The feed rate of the milling head should be in the medium speed range, depending on the panel thickness.
Especially for transparent acrylic sheets, laser cutting is an excellent method to cut acrylic glass to the desired size. The greatest advantage of laser cutting is the appearance of the cut edge. Whereas cutting methods such as sawing or milling usually produce a more or less rough, cloudy cut edge, the cut edge appears polished and smooth through non-contact cutting with a laser. This primarily affects the transparency of the cut edge. The power and speed of the laser depends on many factors. Among other things, whether the acrylic sheets are cast or extruded is a deciding factor. The thickness of the sheet and the power of the laser unit used also affect the cutting speed and quality of the cut edge.
Waterjet cutting offers comparable results in terms of cut quality and flexibility to laser cutting, but can usually only be implemented without problems for larger sheet formats, as the pressure of the waterjet may cause the acrylic sheet to shift or bend under certain circumstances.
The most unsafe method, which is only suitable for low thicknesses, is breaking acrylic sheets. Here, the cut edges are scribed with a scribing tool or a sharp knife and then broken over the edge. However, the risk that the breaking point will not produce the desired result is quite high, so we tend not to recommend this method and mention it only for the sake of completeness.
TIP: It is better to buy your acrylic glass sheets directly cut to size at best prices in our online shop.
A simple cordless screwdriver with a sharp metal drill bit is sufficient for drilling acrylic glass. When drilling holes, however, it is important to note that the sheets should rest on a firm, level surface and that the sheet must not wobble in order to avoid chipping at the drill holes or cracks in the sheet. Do not apply pressure to the drill bit. A medium speed of the cordless screwdriver will give the best results. Too high a speed can lead to too high a temperature, which can cause the drill chip to fuse with the drill hole. Too low a speed can cause chipping and splintering at the edges of the hole.
TIP: Individual hole drilling and shapes made of acrylic glass, we offer with our online laser part configurator.
The installation of acrylic glass panels for patio roofs, carports or as balcony privacy screens is carried out in a similar way to the installation of panels made of conventional glass. Particular care should be taken when screwing the plastic sheets that the screws are not tightened too much, otherwise the sheets can break out at the drill holes. If the sheets are used as glass substitutes for roofing or as shelves in cabinets or showcases, the appropriate thickness should be selected depending on the load or load capacity. In simple terms, the lower the thickness, the lower the load-bearing capacity of the panel. It is important to note that it is not the plastic sheet itself but the substructure that is responsible for the load-bearing capacity.
When mounting on the wall, always use suitable mounting material that is able to bear the weight of the sheet. The weight of the acrylic glass sheets depends on the thickness and size of the blanks and is displayed below the price when configuring your acrylic glass sheets in the blank. For information on the load capacity of the screws and dowels, please contact the respective manufacturers.
Gluing acrylic glass is very simple. Simple solvent-based adhesives, as well as silicones, MS polymers or hot-melt adhesives are suitable adhesives. Before bonding our acrylic glass sheets, the protective film should be removed from the areas to be bonded.
Especially with our special cat-welding adhesive PMMAprofi of our own brand S-Polybond, bonding acrylic glass is child's play. Both acrylic glass with acrylic glass and acrylic glass with other plastics. After the adhesive has cured, the bonded areas are firmly and securely welded together and are absolutely watertight when used correctly. For example, terrariums or aquariums can also be glued by welding the sheets together at the gluing points. Furthermore, the adhesive is completely volatilised after curing, so that this does not have a negative effect on the recyclability of the plastic.
Note: Deep-drawn parts or lasered acrylic glass cannot be bonded with solvent-based adhesives as this will cause stress cracks.
As a thermoplastic, acrylic glass can be excellently thermoformed. By thermoforming, acrylic glass can be brought into almost any shape, which remains permanently intact after cooling.
Temperatures between 150 °C and 190 °C are recommended for deep-drawing. The heating time depends on the total thickness of the acrylic sheet. For simple bends or bending around a radius, even lower temperatures can produce the desired result by heating with a hot air blower. Since PMMA draws moisture from the environment, the sheets should be pre-dried before thermoforming. In addition, the protective film must be removed before thermoforming, as it is not thermoformable.
Acrylic glass is best cleaned with a soft cloth and a neutral cleaner.
Even though the surface of acrylic glass sheets is quite insensitive to scratching, the use of microfibre cloths or scouring pads should be avoided, as these can still leave fine scratches on the very smooth surface. The low chemical resistance of PMMA to solvents can lead to stress cracks on edges and surfaces when harsh cleaners are used, especially if they are based on alcohol or solvents. This can lead to stress fracture and thus render the panel unusable. We therefore strongly advise against the use of such cleaning agents and recommend lukewarm water and neutral household cleaners or soap-based washing-up liquids instead.
Stubborn dirt can be removed with solvent-free benzine or similar. Here, too, care should be taken to use a soft cleaning cloth to avoid scratches.
Acrylic glass can be completely recycled in different ways. If this plastic is separated according to type, new acrylic sheets can be produced from the plastic waste. However, in order to produce transparent plastic sheets from recycled material, acrylic glass must also be sorted by colour and filtered in a complex process. Even small amounts of coloured or opal waste can impair the transparency or colourfulness of the recycled sheets. Through special processing techniques, the polymerisation process can also be reversed, so that acrylic glass can be broken down into the individual raw materials again.
Due to its chemical structure, acrylic glass can be excellently recycled both materially and chemically and can be broken down again into its chemical components by a special processing method in order to produce acrylic glass again by polymerisation. This process is also called chemical recycling of acrylic glass. On the one hand, this saves valuable raw materials for the production of acrylic glass sheets in new product quality, and on the other hand, no further plastic waste is produced.
In material recycling, the plastic waste from acrylic glass is crushed, ground and melted down into recycling sheets, which must be labelled as reclaimed material. Last but not least, the thermal recycling of acrylic glass is also a possible use. Here, part of the energy that has to be used for the production of the acrylic sheets is recovered through incineration. Incineration in waste incineration plants takes place in particular when acrylic glass is not disposed of properly, e.g. via residual waste. However, valuable raw materials are irretrievably lost in this process.
Acrylic glass can be disposed of via the recycling bag or the recycling bin or at the recycling centre. Unfortunately, however, this does not always guarantee proper recycling of the individual plastics, so that incineration in the waste incineration plant cannot be ruled out. Larger quantities of acrylic glass can certainly be sold again to special recycling companies, depending on the care taken during separation.