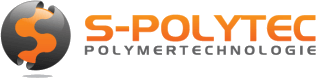
Hard PVC (polyvinyl chloride, PVC-U) is a thermoplastic material with a high chemical resistance. Our PVC sheets are solid and comply with the European Union RoHS guidelines.
Incl. 19% Tax
Incl. 19% Tax
Incl. 19% Tax
Incl. 19% Tax
Incl. 19% Tax
Incl. 19% Tax
Incl. 19% Tax
Incl. 19% Tax
Incl. 19% Tax
Incl. 19% Tax
Incl. 19% Tax
In our online shop we offer you PVC sheets made of rigid PVC (PVC-U) in various designs and colours, cut to size or as a whole sheet in standard format at particularly favourable prices.
Thanks to our cut-to-size configurator for our made-to-measure PVC sheets, quantity discounts are taken into account fully automatically. Simply select the sheet thickness you require from the available thicknesses and enter the dimensions for your PVC cuts in millimetres (not centimetres). The maximum format for our PVC cuts is 2000mm for length and 1000mm for width. Last but not least, please indicate the quantity you require. Based on the total weight of your configuration, we will calculate the most favourable price for you. The total sum, the total weight, as well as the unit price of your cut-to-size pieces is calculated and displayed in real time.
For our standard panels in the 2x1 metre format, the specifications for length and width are not applicable, as these are already specified. For our PVC sheets, you only have the choice of thickness and quantity to calculate the price. Of course, weight-dependent discounts are also automatically calculated for our standard sheets in order to guarantee you the best possible price at all times.
Thanks to a constant stock of our PVC sheets in all offered thicknesses, colours and designs, extremely short delivery times are possible. Due to very good purchasing conditions with our manufacturers, which are not least due to the very high purchase quantity, we are able to offer PVC cuttings at particularly favourable prices. This does not mean, however, that you have to accept a loss of quality. Quite the contrary. Rigid PVC sheets offered by us are produced in Germany in an outstanding quality according to valid EU guidelines. Only 100% new material is used in the production of our sheets and no other substances are added. Therefore, our PVC sheets meet all standards such as REACH (EU Chemicals Regulation), RoHS (Regulation on the prohibition of hazardous substances in the electrical industry) or PAK (Directive on compliance with the limit values for polyaromatic hydrocarbons).
Our PVC sheets consist of solid solid core material and not of sheets with a foamed core (hard foam sheets). In addition, all our sheets are fully dyed through for perfect colours that are identical on surfaces and cut edges. Furthermore, our plastic sheets made of hard PVC do not contain any phthalates (softeners).
Note: All PVC sheets in standard format can also be supplied cut to size on request. Our friendly advisory team will be pleased to inform you about delivery times and delivery conditions.
You need individual milled parts made of PVC? For example perforated plates, housing components or machine covers? With our milling service, completely individual shapes can be realised, if desired with cut-outs, recesses or countersinks for screw connections. Simply send us your design drawing as a DXF or DWG file (alternative file formats: STEP, IGES, AI (Adobe Illustrator) and EPS files) and tell us the required number of pieces per delivery.
We will contact you as soon as possible to provide you with an inexpensive, tailor-made offer including shipping costs, exactly according to your specifications and needs.
Depending on the total dimensions and weight of your order, your PVC sheets will be delivered by a parcel service or on pallets with our partner shipping company. The delivery time for our PVC sheets depends on the product type. If it only concerns PVC cut-to-size sheets that we keep in stock in our production warehouse, the order is usually processed and handed over to dispatch on the next working day. In the case of standard sheets with a format of 2x1 meter, the goods are made available on call, so that delivery times of up to one week are usual.
Before dispatch, all orders are checked for completeness and correctness of the goods. In the case of cut-to-size items, the dimensional accuracy is also checked and then carefully packed so that the goods arrive safely at your premises. We pay attention to sustainability when packing our plastics and therefore we only use fully recyclable packaging material.
Note: Rigid PVC is a technical plastic and as such is supplied without protective film. Therefore PVC sheets should not be used for optically demanding applications. An exception are the transparent PVC sheets (PVC glass). Here a protective film is applied on both sides, which can be easily removed.
Typical applications of PVC sheets are in tank construction or apparatus engineering, the manufacture of linings and composite construction, as well as use in air conditioning and ventilation technology, and the manufacture of ceiling and wall elements.
Due to the low flammability of PVC, this plastic is very often used in the field of fire protection. The areas of application in this field range from small signs for extinguishing systems, to flame-resistant glazing made of transparent PVC glass, to large-area panelling of machines, electrical equipment and walls, where fire protection regulations require flame-resistant materials.
The classification as flame-retardant plastic is also often required in many areas accessible to the public. Not only to prevent vandalism. For this reason, PVC is also very often used for printed or inscribed advertising signs, for glass replacement made of plastic, e.g. at bus stops or telephone booths.
However, PVC is not only flame retardant, but also has a high surface hardness and good resistance to acids and alkalis. In addition, rigid PVC is also highly resistant to fats and oils. This plastic is therefore used both in container construction for chemical tanks and in pipeline construction, for example for sewage pipes.
PVC is also used as pipe in the electrical industry. For example, as protective pipes for surface cabling, as well as for empty pipes for flush-mounted cabling. Due to its excellent insulating properties, PVC is also very often used for insulators, junction boxes, socket covers, light switches, cable insulation, to name but a few examples.
The abbreviation PVC stands for polyvinyl chloride. PVC is an amorphous, thermoplastic material and in its natural form transparent with a very slight blue tinge. It is produced in a radical chain polymerisation of vinyl chloride.
PVC is one of the most widely used plastics and is used in more different areas of application than almost any other plastic. Only the two technical polymers polyethylene and polypropylene are used even more frequently due to their diverse properties. However, PVC is not all the same and so a basic distinction must be made between two types.
Rigid PVC, also abbreviated as PVC-U. The U stands for unplasticized which simply means that the plastic is not enriched with plasticizers. As a result, hard PVC not only has a high surface hardness, but also a higher density and is considered to be comparatively brittle. By adding additives, however, the properties of PVC can be optimised, for example to achieve higher impact resistance or resistance to UV radiation and weathering.
With soft PVC, PVC is made more elastic and plastic by adding fillers in order to make this plastic suitable for many more applications. Hence the abbreviation PVC-P, where P stands for plasticized. Phtalates (e.g. bis(2-ethylhexyl)phthalate) are mainly used as additives. The so-called plasticizers of PVC repeatedly cause discussions about the carcinogenic effect of phthalates. Over time, the plasticizers evaporate and gradually diffuse out of the plastic. This makes the material increasingly brittle over time. New substances are being developed here in Germany and phthalates are being substituted by other additives.
Note: All PVC sheets offered by us are made of rigid PVC without plasticizer.
PVC sheets made of rigid PVC are characterised by a very high surface hardness. The solid sheets are extremely rigid and have a good resistance to chemicals, but are not resistant to solvents, which is why this plastic can also be bonded very well with appropriate adhesives.
Probably the most important property of PVC is its low flammability. PVC does not continue to burn after the flame is removed, so that the criteria for classification according to DIN 4102 B1 are fulfilled. Only thicknesses of 1mm - 4mm were tested for this DIN standard, but the plastic remains the same even at higher thicknesses, so that here too there is a low flammability. In addition, all of our hard PVC sheets with a thickness of 1mm or more comply with the UL94 V0 standard, which is also considered flame-retardant. This means that PVC can be used excellently in areas accessible to the public, where fire protection requirements must be met.
Note: Detailed information on the physical properties of our PVC sheets can be found in the respective product description and the corresponding data sheets.
PVC sheets can be processed in a similar way to wood and so tools for wood processing can be used. The sawing or milling of rigid PVC sheets does not require any special tools, so that PVC blanks can be cut into the desired format without any problems. Experience has shown that a conventional circular saw or a jigsaw with a medium-sized saw blade gives the best results. Especially with PVC, it is important to pay attention to the correct speed. This speed, as well as the feed rate, should be rather low in order to avoid excessive heat development at the cutting edge. If the rpm is set too high, the surface of the cutting edge can burn and lead to the formation of hydrochloric acid, which attacks the saw blade and can lead to rapid rust formation.
Warning: Cutting with a CO2 laser is not possible for plastic sheets made of PVC due to the heat generated. The hydrochloric acid produced by heat attacks the laser system and can, in the worst case, render it unusable.
Drilling holes or countersinks in the hard PVC sheets is very easy with a standard metal drill and a cordless screwdriver. As with any plastic, however, the speed of rotation of the device used should be selected quite low. Due to the high surface hardness of the PVC-U, it is recommended to mark the holes with a centre punch to avoid possible slipping of the drill. This enables very precise positioning of drill holes. Thread cutting can also be applied to the hard plastic panels in order to screw the panels together or to other substructures with threaded screws.
TIP: With our milling service, we can not only cut your PVC sheets to any desired shape, but also drill holes.
PVC sheets can be mounted in many different ways. Both the large-area bonding of PVC-U panels with an assembly adhesive, for example as fireproof wall cladding, and by screwing them to a substructure or flat surfaces. For cladding of ventilation systems or fire protection systems, screwing is a very common method. Control cabinet components, insulating partitions or flame-resistant housings are also usually screwed together. When screwing, however, the screws should not be tightened with too much force. In this way, break-outs or cracks in the comparatively brittle plastic can be avoided.
PVC is an easy-to-bond plastic and can be bonded excellently with common solvent-based adhesives, such as our rower L530. Our assembly adhesive Parabond 600 is also well suited for gluing PVC panels as large-area cladding. Bonding, laminating and laminating with digital printing or coloured films is also no problem with the solid rigid PVC panels.
Although PVC can be glued excellently, in many cases welding is the preferred method of bonding PVC permanently and securely. With a suitable PVC welding rod, plastic welding of PVC is not a great challenge, but requires some practice. Choosing the right temperature also plays a very important role in welding, because if the temperature is chosen too high or the material is heated too long, the surface of the joined parts or the welding rod will burn. On the one hand, this affects the visual appearance, but above all it worsens the quality of the weld seam. In addition, hydrochloric acid is produced when the surfaces burn, which has a strong pungent effect when inhaled. The ideal air temperature for PVC welding is between +250°C and +280°C.
PVC belongs to the group of thermoplastics and as such can be excellently thermoformed. The production of prefabricated plastic parts in deep-drawing processes is frequently used in aircraft construction or in the interior fittings of railways. It is important to note that in this case, it is essential to maintain the temperature and heating time in order to avoid burning the sheets. The ideal temperature range for thermoforming rigid PVC is between 90°C and 140°C. PVC is therefore, similar to polystyrene, already thermally formable at very low temperatures.
Rigid PVC does not decompose even over decades and is therefore not harmful to water organisms or the air. In order to dispose of PVC in an environmentally friendly way, this plastic must be treated professionally and should not end up in a landfill.
Although PVC can be thermally recycled, i.e. incinerated to generate energy, its calorific value is very low and the residues are classified as hazardous waste. In addition, the cost of special filtering equipment to filter out the hazardous gases produced when PVC is incinerated is very high. So not really a useful recycling method.
Recycling, on the other hand, can be done in two ways. On the one hand, the valuable recycling of PVC, in which the plastic waste is remelted and processed into new plastic sheets, rods or pipes. The resulting PVC regenerates the material, so that crude oil and other raw materials are no longer needed. The second method is raw material recycling. Here, hard PVC is split into its chemically usable materials by means of very high temperatures. This quite complex and cost-intensive process is also called pyrolysis and is used especially for mixed plastics.
Disposal via the yellow bag or, depending on the region, the yellow bin is allowed, but it can never be 100% guaranteed that PVC is actually recycled and does not end up in the incinerator. The best and safest method for environmentally friendly recycling is to collect PVC by type and dispose of it at the recycling centre. Unlike many other plastics, PVC has its own recycling code 03 for polyvinyl chloride.