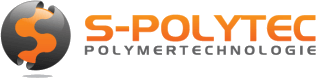
We offer welding wires and welding rods for almost all plastics in various designs and colors as cheap meter product starting from one meter. So you can order the amount you need directly to match your needed plastic plates and start directly with the plastic welding.
Plastics are usually not only used as a pure sheet and therefore it is often necessary to join several plastic parts together so that a permanent and secure joint is created. In many areas of application, bonding the joined parts can be quite sufficient for the intended use, but bonding is not always a suitable method. Furthermore, there are also plastics that are difficult or impossible to bond due to their chemical resistance.
Whenever bonding with a suitable adhesive cannot meet the requirements for joining the plastic parts, welding the plastics with a suitable welding rod or welding wire can be a suitable method for producing a firm, secure and tight joint between the individual parts.
Basically, it does not matter for welding plastics whether they are welded with a welding rod or with a welding wire, as they are made of the same plastic. While plastic welding rods are usually offered on a spool or as a loose roll as kilo goods, welding rods are rigid rods, usually with a length of 1 metre or 2 metres. When rather a welding rod or a welding wire is used depends on the one hand on the availability, because not every plastic is available in identical design and thickness both as welding rod and welding wire, and on the other hand on the personal preferences in processing the welding rods or wires. While some prefer to carry out large welding seams without gaps using a welding rod, others prefer to work with a more manageable welding rod, which is easier to guide and track because it is straight, but only shorter welding seams are possible here without having to reattach another welding rod.
Since our welding rods and welding wires are made of the same plastic as the plastics to be welded, the physical properties of the welding rods also correspond to those of the plastic sheets of the same type. Temperature application ranges, softening temperatures, physical density or even UV and weather resistance are properties that relate to the plastic. It does not matter whether it is a solid plastic sheet, a hollow rod, a solid rod or even a welding rod or welding wire.
As each plastic has its own characteristic values for the respective properties, the physical properties for our welding rods and wires can be found in the description of the respective plastic category for our welding rods and wires.
The right welding rod
For plastic welding, the appropriate welding rod must always be used. Plastic sheets made of polypropylene should therefore only be welded with a welding rod made of polypropylene. Even with subordinate types, such as is the case with polyethylene (PE-HD, PE-HMW), the correct welding rod for the plastic should always be used to ensure perfect welding of the plastics. The colour of the welding rod plays no role in the quality of the weld seam and only affects the appearance of the weld seam. Whether the welding rod selected is round, oval or triangular also plays only a subordinate role for the welding seam itself, but can make the welding process itself easier.
The right welding temperature
Every plastic that is suitable for plastic welding has its own welding temperature, which depends on the softening temperature of the plastic itself. The temperature should be selected depending on the plastic so that both the welding wire and the surfaces to be welded are sufficiently heated so that they begin to melt. If the welding temperature is too low, no solid weld seam can be produced, as the fusion of the plastic sheets with the welding wire cannot take place. If the temperature is too high, the plastics can burn, which again affects the quality of the weld. Which temperature should be selected for which plastic, please refer to the respective specifications for the welding temperatures of the respective plastic welding wire or plastic welding rod.
The right welding machine
Which welding machine is used to weld plastics is not decisive for success, but a distinction must be made between different welding machines for welding plastics.
For simple welding seams, or for the occasional welding of plastics, the so-called welding pistons are suitable, in which, simply put, the metallic tip heats up and initiates the melting process through direct contact with the plastic. Welding pistons are also excellent for welding cracks or fractures, as the tip of the piston dips into the crack and the welding wire is melted almost flush into the surface crack. For large or frequent plastic welding jobs or long welds, however, this welding device is only suitable to a limited extent, so that other welding devices could be used more efficiently.
A very common method is welding with a hot air tool, in which a heating coil is heated to the set temperature. A small fan ensures that air flows past the heating coil, heats up and flows out at the nozzle of the hot air tool. The principle of operation of the hot air welder is comparable to that of a hair dryer, but with the hot air dryer significantly higher temperatures are reached, which are required for welding plastics. Such hot-air welding devices are available in a wide variety of designs and quality levels, ranging from the small purse to the professional version for long-lasting welding work. Often, different attachments (also called welding shoes) can be attached to the nozzle, which concentrate the outflowing hot air to a greater or lesser extent. Some of these attachment nozzles have a guide eye through which the welding wire is guided to ensure exact guidance and simplified tracking of the welding wire within the weld seam.
As the most professional, but also most expensive variant, hand welding extruders are used in plastic welding. In simple terms, with the hand extruder the welding wire is melted inside a screw conveyor and automatically fed. During the welding process, a hot air nozzle heats the plastic surfaces to be welded to a preset temperature. The screw conveyor discharges the molten welding wire at the outlet nozzle and a welding shoe, which has to be selected in advance depending on the type and shape of the weld seam, gives the weld seam its final appearance. When using a manual welding extrusion device, however, welding rods are generally rather unsuitable, as these do not ensure gap-free tracking of the welding rod.
The perfect weld seam
The perfect weld seam depends primarily on the factors already mentioned. On the one hand, the welding rod itself, the welding temperature and the heating time are decisive for the quality of the weld seam. But even if these criteria are fulfilled, it always requires a little practice to weld plastics in such a way that the joint fulfils its purpose and looks visually appealing without requiring a great deal of reworking, either through repeated welding or grinding.
On request we also supply
Plastic welding rods and welding rods made of plastic are used wherever adhesive bonding as a joining method is out of the question due to the requirements on the joint, or is not possible or only possible with difficulty due to the properties of the plastic. Particularly in branches of industry where there are high demands on the joining of plastic parts in terms of durability and/or tightness, plastic welding is a common practice and is used, for example, in container construction for chemical containers or lining troughs.
Plastic welding is also very often practised for repairing breaks and mending cracks in plastic parts, for example to repair housings and covers in mechanical engineering.
Since our welding rods and welding rods are made of unmixed plastic and have the same properties as solid plastic sheets made of the same material, they are also treated like the plastic itself when disposed of and can be sorted and collected for the recycling process to make plastic sheets or welding rods from reclaimed material. This also applies to welded plastic sheets, unless an unsuitable welding rod made of the wrong material was accidentally used to weld the sheets.