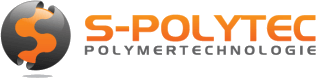
With our aluminum constructionprofiles, we offer the right aluminum profile for countless projects in 2-meter and 1-meter lengths, or precisely cut to your desired dimensions. In addition to the made-to-measure profiles, we also offer a wide range of accessories for mounting and connecting the profiles, as well as countless fasteners to suit the respective groove widths for a complete system that leaves nothing to be desired.
Incl. 19% Tax
Incl. 19% Tax
Incl. 19% Tax
Incl. 19% Tax
Incl. 19% Tax
Incl. 19% Tax
Incl. 19% Tax
Incl. 19% Tax
Incl. 19% Tax
Incl. 19% Tax
Incl. 19% Tax
Incl. 19% Tax
Our anodised aluminium construction profiles offer a flexible modular system that allows for quick adjustment and expansion of constructions. Whether for machine frames, shelving and storage systems or individual special constructions. Due to the modular structure, constructions can be adjusted and expanded as desired at any time. This is particularly useful when requirements change over time.
Our construction profiles are precision-made and designed to be connected with simple means. This saves time and reduces the need for specialised knowledge and tools during assembly. The wide range of connecting elements, castors and feet, covers, hinges and other accessories is precisely matched to the profiles and ensures a high level of accuracy of fit, which in turn ensures stable and long-lasting constructions.
With us, you only pay for what you order – this also applies to the profiles in the cut!
We offer maximum flexibility with the option of ordering the profiles in the standard length of 2005mm, as well as in 1-metre lengths, and in custom lengths cut to the millimetre. The price is calculated dynamically based on the weight, because, as is usual for raw materials, raw materials such as aluminium or plastic are not traded by area or length, but by weight. When calculating our prices, we automatically take into account quantity discounts for larger order quantities of the same profile, as well as for several similar cuttings. The biggest advantage for the profiles in the cutting is that the sections that remain after cutting are not calculated and, if possible, reused.
We place the greatest emphasis on quality and compatibility in our aluminium system profiles.
At first glance, all construction profiles look the same. The difference lies in the details. Starting with a high-quality aluminium alloy, which has excellent strength and stability, and continuing with the satin gloss surface finish. This is created during adonisation and contributes to an even, smooth colouring, but also improves the already very good resistance to corrosion. This means that the profiles can be used permanently in outdoor areas, even in damp environments or in the most adverse weather conditions. To protect the flawless appearance from damage during transport, processing or assembly, our profiles are covered with a strong protective film. This can be easily removed from the profile without leaving any residue. We have decided on the most common sizes, with equally common groove widths, to ensure that the profiles can be easily combined with those of other manufacturers.
In the case of fittings that are inserted into the grooves for assembly, it is necessary to check in individual cases whether the width and depth of the groove are suitable. This applies to T-slot nuts, T-slot nuts with springs and balls, hammer head screws, internal corner connectors and profile connectors or 3-way corner connectors. On the other hand, for all system components that are attached to the profile from the outside, only the groove width or total width of the profile is important, so that, with the exception of a very few special forms, any construction profile can be combined, regardless of the manufacturer, design or type. This is particularly useful when making changes or additions to existing constructions made from the popular system profiles.
Construction profiles are particularly suitable for building stable, modular structures and are characterised by their flexibility and ease of use. A typical feature of these profiles is smooth surfaces interrupted by groove-like indentations. The most common form of groove is the so-called T-slot, which allows the use of connecting elements such as slot nuts, connectors and covers. This makes it easy to adjust, extend or modify profiles without the need for special tools or additional manufacturing steps. The system is also suitable for subsequent modifications or extensions. The central concept of construction profiles is their modularity. The profiles can be combined in any way you like, offering great flexibility when designing structures. You can build very different structures with the same profiles, from simple shelves to complex machine housings. Construction profiles are mainly made of aluminium. Less common, however, are construction profiles made of steel, plastic or composite materials. The advantages are quite simple. Aluminium is light, strong, does not rust and is very easy to work with.
We use the most common type of square cross-section for our aluminium construction profiles, in which all four surfaces have the same width. These are each divided lengthwise in the middle by an open groove. The width of the groove depends on the size of the profile. The small profile measuring 20mm x 20mm has a groove that is 6mm wide. The two wider profiles have a groove width of 8mm. The surfaces of our profiles are anodised, which makes them even more resistant to corrosion and also creates an aesthetically pleasing surface.
At first glance, the layman can hardly distinguish between the two system profiles. The range of applications is comparable, as are the manufacturing processes and the materials used. Even the fasteners and assembly parts, which are used to turn the profiles into flexible constructions that can be adapted to the situation, are very similar in type and variety. To put it simply, these are two different systems. However, this does not mean that they cannot be combined with each other.
The main differences can be seen in the profile shape in cross-section. Profiles of the I-type of the item® system, as well as profiles of other manufacturers and brands based on it, can be identified by more rounded edges and rounded slots. In the Bosch Rexroth® profile system, i.e. the B-type, the outer edges of the profiles are rounded only in a very narrow radius, which makes them appear much more angular. The shape of the grooves is also angular here. As a result, T-slot nuts for the I-system are not suitable for B-profiles and vice versa. The same applies to T-head bolts, internal profile connectors and the like. In other words, anything that can be used for assembly within the slot.
Profiles in 20mm, 30mm, 40mm, 50mm and 60mm are common in both systems. The B system also includes a 45mm profile as standard. Of course, there are also some special solutions that deviate from a square cross-section, or have grooves that are only open on two or three sides, whereas the remaining sides have a closed surface. In addition to the many variants, there are countless other manufacturers and brands, including us, that more or less follow one of the basic systems. Not all products are compatible, which is why some manufacturers even rely on completely proprietary solutions that can only be processed with the associated system accessories
Our construction profiles are made of solid aluminium using the extrusion moulding process, as are those of most other manufacturers. Aluminium offers a number of advantages over other materials. First and foremost, it is comparatively very light, weighing only about a third as much as steel. In addition, aluminium is much easier to cut or drill than iron, steel or alloy steel. The decisive factor is the exact alloy from which the profiles are made. We use a high-quality EN AW 6063 T5 aluminium for our construction profiles that ensures a good balance between material hardness, modulus of elasticity and yield strength, so that the profiles can be used for highly stable, resilient constructions of all kinds. Added to this are good plasticity and excellent corrosion resistance. In particular, the tendency to stress corrosion cracking, excellent weldability, corrosion resistance and cold workability contribute to the fact that 6063 aluminium is used for countless semi-finished products.
Aluminium is also a good heat conductor, which means that thermal energy is quickly transferred. In the temperature range from -80 to +150 °C, the material properties remain largely constant. Prolonged exposure to high temperatures above the continuous operating temperature affects the strength and hardness of the material and should therefore be avoided. The melting point of aluminium is approx. 615 - 655°C, which is significantly lower than that of stainless steel. The low melting point makes aluminium very suitable for casting, which also has an impact on the costs for the production of extruded profiles and is another reason why aluminium construction profiles are so widespread. Although its electrical conductivity is only around 60% of that of copper, aluminium is still a good electrical conductor. This is particularly advantageous for earthing machines and systems and, in combination with a residual current circuit breaker (FI for short), can help to increase safety against electric shock. Electrostatic charge can also be easily discharged via the aluminium profiles.
The load-bearing capacity of a construction profile depends on two essential factors, which must be taken into account depending on the specific application in order to construct a stable and sustainable structure. The profile size and the length between two mounting points. A construction profile increases in load-bearing capacity the higher the profile thickness. This does not necessarily mean the external dimensions of the profile, because in addition to standard design construction profiles, there are also extra-light or extra-stable designs in which the material thickness of the individual aluminium webs is thinner or thicker. The weight per metre can serve as a rough initial indicator here. The heavier a metre of the profile is, the more material, and thus the more solid, is used for the profile during production. A higher profile thickness is also logically associated with improved bending stiffness and torsional rigidity. Usually, the material thickness of a profile increases with increasing size. This means that a standard profile in 30x30mm groove 8 is generally stronger than a standard profile in size 20x20mm with 6mm groove width. The 40mm version is usually even more stable. We have already briefly outlined the relevant indicators for comparison and for determining the effective load capacity. These are the flexural rigidity, which is given in the technical data sheets as the flexural resistance moment (Wx, Wy) and the resistance to deformation of the cross-section area or twisting around its own axis, which are referred to as the moments of inertia (Ix, Iy, It). The higher these values are, the more stable a profile is and the higher the load can be for an identical construction.
NOTE: The fact that the values for the X-axis and Y-axis are identical is due to the fact that the profiles are symmetrical in cross-section and have the same edge length, profile thickness and web arrangement. This is no longer the case for profiles with a groove closed on one side or in a rectangular format.
The section modulus about the X or Y axis is a measure of the resistance of a cross-section to bending about the respective axis. This value is used to calculate bending moments and determine the bending stress of a profile and provides information on whether permanent deformation is to be feared when a load is applied. If the calculated result is higher than the yield strength of 292N/mm2, a deformation of the aluminium is to be expected. A lower value, on the other hand, means that the load will not have any permanent effects on the straightness of the aluminium profile.
The moment of inertia around the X or Y axis is an important value for calculating the deflection caused by the dead weight or an additional weight load, for example the load-bearing capacity of a shelf or a base frame for a table or a bed frame. A higher moment of inertia will bend less under the same load. However, the formulas for calculating the deflection of a profile require a few more calculation variables. The weight force, i.e. the force that acts through the earth's gravity in relation to the dead weight and the specific length of the profile, is one of the parameters that must be calculated separately. The expected weight must first be converted from kilograms to newtons using a simple formula. Once these values have been determined, the exact values of the respective deflections can be calculated using further constant factors.
TIP: At first glance, the formulas seem daunting and confusing, but you don't need a PhD in mathematics to calculate the deflection. To explain the calculation in detail, we have written a separate blog post in which we explain each required parameter, the formulas for weight and load conversion, and the deflections step by step.
When applying the load, a distinction must therefore be made as to whether there is an additional weight load or whether only the dead weight of the construction is to be taken into account. In this case, a distinction is made between deflection due to dead weight, deflection due to applied weight and total deflection, which is the sum of both values. Depending on the profile design and the expected deflection, intermediate struts or supporting posts may be advantageous or even necessary.
A bed frame in the interior of a camper van is a realistic example. It is a popular method of converting a van from a transporter to a camper van. Construction profiles are perfectly suited for such projects due to their versatility, flexibility and low weight. Let's assume that the bed is to be built with construction profiles measuring 30x30mm with a lying surface of 100x200cm. A slatted frame and a mattress should of course be placed on the substructure. While the slatted frame also ensures improved load distribution on the construction, it is also a weight that acts on the construction. On top of that comes the mattress, the bedding and, last but not least, your own body weight. The latter in particular is not set in stone and can vary quite a bit. It should also be noted that another person might stay overnight and the bed frame should not collapse under the load. If you now take into account the additional strain caused by movement, after all, it has been proven that you turn over several times during the night, you should play it safe. One or two additional struts should be added to the long side of the frame. These also prevent the slatted frame from caving in. In addition to the four feet at the outer corners of the rectangular frame, we recommend two to three support posts under the 2-metre profile. Better safe than sorry. The practical thing about this is that you can easily integrate drawers or cupboard doors at this point. This is how useful storage space is created. The larger 40mm profiles add a little more weight, but here the intermediate struts and supporting posts can be reduced or even completely dispensed with.
Cutting Aluminium profiles can be shortened with a hacksaw with a fine metal saw blade. However, this manual effort can be tedious. A cutting-off grinder or a jigsaw are also suitable, but they are not nearly as precise and clean as the use of a cross-cut saw to cut the profile to size. A crosscut and mitre saw is almost indispensable, especially when the profiles are mitred at a fixed angle. For aluminium, you will need a saw blade for metal in any case. When sawing, the cut must be made at a low speed. When using a compass saw or reciprocating saw, the pendulum action must also be switched off. Otherwise, there is a risk that the aluminium will discolour due to excessive heat build-up. The robust protective film, which is designed to protect the surfaces from damage during transport and processing, naturally also serves its purpose when shortening the profiles. However, the sawdust then sticks to the self-adhesive surface in the area of the open grooves.
When sawing aluminium profiles, we recommend wearing protective goggles and work gloves, as both the sawdust and the burr on the cut edges can be very sharp. The edges should therefore always be deburred after sawing to avoid cutting injuries.
Drilling As a light metal, aluminium is very easy to drill. All you need is a cordless screwdriver with an HSS drill bit of the required diameter. To drill the hole exactly where you want it, without the drill slipping on the smooth surface, we recommend using a drill bit with a self-centring tip. Alternatively, you can gently hammer the position into the surface with a centre punch. However, drilling is not normally necessary for construction profiles, as the constructions are created using brackets and connectors. Attachments can also be mounted using the extensive range of mounting accessories with sliding nuts and screws. The diameter of the clearance hole in the centre of the profile cross-section is also selected so that a thread can be directly screwed in with a tap. For example, to mount a caster, bracket or stand at this point. Additional drilling of the core hole is therefore not necessary.
Screwing Construction profiles are screwed to the so-called fittings in order to construct a wide variety of structures. These are special accessory parts such as profile connectors, slot nuts or hammer head screws. A distinction is made here between internal mounting and surface mounting. For internal mounting, the connectors are inserted into the slot and fixed in the slot with small grub screws. Typical examples are the extension of construction profiles or the corner connection of two profiles with an internal angle connector. For mounting on the profile, the angle brackets or hinges are attached with suitable screws and sliding nuts. The latter are also inserted into the groove, but the attachment part is visible on the outside of the profile. Depending on the fastener, different tools are required. For grub screws, socket head cap screws and countersunk head screws, a suitable size Allen® key is needed. When mounting with carriage bolts and nuts, a spanner in the appropriate size is required.
Another type of screw connection is to screw directly into or through the profile. To do this, a hole must be drilled. However, this loses the advantages of flexible adaptability and the visual integrity of the profile. Whether the hole also has to be threaded depends on whether a threaded screw is to be screwed directly into the profile or whether it is to be fastened on the back with a nut. The pitch circle of the hole also depends on the type of fastening. When mounting with a nut, the hole must correspond to the size of the screw diameter or be larger, but smaller than the screw head diameter. If the threaded screw is screwed into the aluminium of the profile, a smaller hole must be drilled and a tap used to cut the thread according to the type of thread. However, there are also self-tapping screws for aluminium that have a tip similar to a drill bit and cut through the metal. Additional drilling is then not necessary. However, a hole in the profile surface cannot be avoided even with self-tapping screws.
Extending Extending profiles for larger constructions is usually done with internal profile connectors that are inserted into one or more grooves and fastened with small grub screws. It is important to use the correct size of profile connector to match the groove width and depth. This is undoubtedly the simplest, quickest and most cost-effective method, as no special tools are required. A standard Allen® key of the appropriate size is sufficient. For this reason, we offer the appropriate connector for each of our construction profiles. A connection with a threaded rod through the through-hole is much less common, but also results in a stable connection between two profiles. To do this, a thread must be cut into the through-hole of all profiles that are to be connected in this way. This method can be used not only to connect two similar profiles, but also profiles in different sizes or different systems with different slot dimensions, as long as the thread in the through-hole has the same diameter. Welding is also a method, but it is only partially suitable because the profiles are difficult to reach with the recessed slots due to their special shape. Furthermore, welding requires both the necessary equipment and the skill to perform a welded connection on aluminium.
Adhering Adhering construction profiles is not one of the most frequently used processing methods due to the large number of fittings required for connection and assembly, but it is certainly possible. When choosing the adhesive, care must of course be taken to ensure that it is not only suitable for bonding aluminium, but also for the material to which the profile is to be bonded. For aluminium to aluminium bonding, we recommend our two-component adhesive MA300. This is also suitable for a wide range of plastics, including ABS, ASA, PVC and acrylic plastics. An MS polymer such as our Parabond 600 also has an extremely strong bond with aluminium and is very suitable for bonding the profiles to building materials on walls, floors or ceilings. These can be sand-lime brick, plasterboard, wood, MDF, tiles and much more. For smaller bonding jobs, for example to glue small objects, covers or circuit boards to the profiles and attachments, a superglue based on cyanoacrylate is well suited. If you are in a hurry, we recommend the MULTIfix by our own brand S-Polybond. For particularly strong bonding, our STRONGfix is an excellent choice.
Coating The simplest form of surface coating is to stick a film onto it. This is very easy to do on such smooth surfaces. A scalpel or cutter knife can be used to cut away the excess film along the groove. This is a very quick and cost-effective way to change the surface colour of the construction profiles. Films are not only available in every conceivable colour, but also in wood, concrete or rust finishes, or individually designed with patterns or colour gradients using digital printing. For untreated aluminium, powder coating is generally also a good and high-quality solution for colouring the surfaces. However, this also applies only to the surfaces of construction profiles that are visible from the outside, because it is almost impossible to apply the coating powder evenly in the grooves. Anodised aluminium also requires the surfaces to be pre-treated to ensure that the coating adheres well. Furthermore, powder coating involves a greater amount of work and is also significantly more expensive.
Varnishing In principle, it is possible to paint the construction profiles, but the surfaces are anodised. This means that the hard oxide layer, which is created by anodic oxidation, must first be sanded down. However, this cannot be done with simple sandpaper. Sandblasting or glass bead blasting is the most suitable method, but it is quite expensive and involves disproportionate costs for the specialist company. After removing the anodised layer, the surfaces must be thoroughly cleaned and degreased, because even fingerprints on the profile can reduce the adhesion of the paint. A primer is highly recommended to ensure the adhesion and durability of the paint. However, there are also countless manufacturers that offer two-component paints that already contain the adhesion promoter. The paint can be applied to the very smooth surfaces with a brush. However, significantly smoother and therefore better results can be achieved with a foam paint roller or a paint spray system.
NOTE: We offer the construction profiles in the standard length of 2 metres. However, the actual production length of the extruded profiles is 2005mm. This plus tolerance is due to the fact that in this way a length of at least 2 metres is always ensured and also allows us to cut the profiles into two individual 1-metre lengths. This would not be possible with a production length of 2000mm, as the cutting thickness of the thick saw blade would also have an effect and one profile section would therefore be too short.
Construction profiles made of anodised aluminium do not require any special maintenance. The surfaces are smooth, so dirt does not adhere to the surface and therefore only occasional cleaning by wiping the surfaces may be necessary. Of course, the location and purpose of use are also important here, because a shelf in a merchandise management room will get less dirty than a construction in an unprotected outdoor area that is exposed to all kinds of weather and environmental influences, such as rain, pollen and bird droppings. A cloth dampened with clear water, soap solution or mild household cleaner is best suited for cleaning. The cloth should be soft and lint-free. Abrasive cleaners or coarse sponges are not recommended, as these can damage the anodised surfaces over time.
Water can collect in the grooves of the grooved profiles. This can be due to a wet cloth during cleaning or precipitation. Although this has no effect on the material, it may be undesirable in the case of constructions for electrical devices and machines, for example. However, such water accumulations within the groove can be easily absorbed by wiping with a dry cloth in the lengthwise direction.
If the grooves of the construction profiles are not closed with cover strips, dust can collect in the grooves over time. However, the grooves can easily be cleaned with a vacuum cleaner with an attachment nozzle. Larger accumulations within the grooves can be quickly removed with a fine brush or a soft cloth.
Our profiles are made of a solid, high-quality aluminium alloy that is extremely easy to recycle. The effort required to melt down this valuable raw material is kept to a minimum due to its comparatively low melting point. Small quantities, known as household quantities, can be disposed of together with product packaging such as tubes, tins or aluminium foil in the yellow sack or recycling bin, so that they can be recycled and separated from plastic packaging. Larger quantities, on the other hand, can be taken to the local recycling centre or given to a scrap metal collector. The latter are often even willing to pick these up if it is worth their while. Normally, the disposal of aluminium is free of charge and in some cases this can even be done in return for a small fee through the purchase.
The assembly materials are also of high quality. Depending on the design, these are rustproof stainless steel, carbon steel with nickel-plated or galvanised surfaces, or plastics. When selecting the materials, we made sure that they could be recycled as far as possible or completely. This is done by melting and re-casting the T-Slot Nuts, T-Bolts or Cross Tees, so that new bolts, nuts or completely different products can be made from the metals. The end caps, hinges and plastic cover strips are also excellent for recycling. However, it should be noted that, as usual with recycling, the materials must be separated by type. For this reason, we have listed the material from which all our articles are made in detail in the technical specifications.