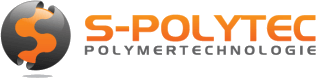
We offer you high-quality aluminium profiles for facade panels in various designs as end profiles or for erecting substructures of facade claddings at very favourable prices from one metre profile length.
Incl. 19% Tax
Incl. 19% Tax
Incl. 19% Tax
Incl. 19% Tax
Incl. 19% Tax
Incl. 19% Tax
Incl. 19% Tax
Incl. 19% Tax
Incl. 19% Tax
Incl. 19% Tax
Incl. 19% Tax
Our HPL panels are often also used for facade cladding. In order to make this area of application possible, we offer you not only the matching assembly material, as well as various drills, but also high-quality aluminium profiles at very favourable prices in our online shop.
In the case of aluminium profiles for our plastic sheets, a distinction must be made between edge profiles for the visual enhancement of cut and butt edges and load-bearing profiles for the erection of substructures. However, these differ not only in the applications for which the profiles are more commonly used, but also in the material thickness. While the substructure profiles have a thickness of 2mm, which results in the very high load-bearing capacity, the end profiles are manufactured in a thickness of 1mm to ensure the lowest possible pleasing edge.
NOTE: Pay attention to the clamping range of the edge profiles, because we offer the aluminium profiles optionally in 6 mm and 8 mm versions, e.g. for our HPL panels in the corresponding thickness. This differentiation does not apply to profiles for the substructure. These profiles can be used universally for our HPL panels in 6mm and 8mm as well as for many other facade panels.
Aluminium is not only weatherproof and rustproof, it is also very easy to work with. A standard saw with a metal saw blade is sufficient for cutting. The end profiles in particular can be cut very easily by hand. However, for an optimal cutting result, especially for mitre cuts, we recommend using a mitre saw or cross-cut saw with a saw blade suitable for aluminium.
Cladding panels are usually mounted on a substructure made of wood or aluminium with a gap between the panels. However, this has the disadvantage that the cut edges of the cladding panels are visible. Especially in the case of HPL panels, where the core is usually made of brown kraft paper, the cut edges can be concealed with high-quality aluminium edge profiles. Another advantage is that slight edge chipping from cutting the panels is thus covered. These usually occur when the hard HPL sheets are not sawn with a pre-cut, as is customary in our company, to ensure perfect cut edges.
Aluminium profiles also offer a significant advantage in terms of thermal insulation, because the required panel spacing creates a gap through which cold (or warm) air can pass. This weak point is also known as a cold bridge (synonymous with a thermal bridge), which can have a negative effect on facade insulation. By using edge profiles, the expansion gap between panels is completely covered so that the efficiency of the insulation can be permanently improved.
However, the aluminium profiles are not only suitable for facade cladding with HPL or fibre cement panels, but can also be used in countless application areas indoors and outdoors. The prerequisite is that the clamping area corresponds to the panel thickness used, regardless of whether it is facade panels, plastic panels, wood or even tiles.
Our aluminium edging profiles are versatile. Primarily, these profiles are used to cover cut edges of facade panels where no other panel is adjacent. However, the high-quality profiles in aluminium-silver are also excellently suited as optical finishes for partition walls, kitchen backsplashes made of HPL or wall tiles with a thickness of 6 mm or 8 mm. The visually valuable profiles can also be used in furniture construction to cover cut edges of veneered chipboard. Especially with thin-walled wood or plastic panels, the bending stiffness can be significantly increased with the stable aluminium profiles. The profiles are very easy to attach by gluing with an assembly adhesive. In addition, the profiles can also be drilled with an HSS drill in order to screw them to the corresponding panels.
Corner profiles are used, as the name suggests, to cover two facade panels that are adjacent to each other at right angles. Especially with light-coloured facade panels such as our white or light grey HPL panels, the dark core can be effectively covered in this way, whereby a more pleasing appearance can be achieved. In addition, the risk of injury from cutting at the often sharp cutting edges is considerably reduced. In addition, corner joints of facade cladding in particular represent a cold bridge, because usually insulation materials that are installed behind the facade cladding cannot be used all the way to the edge, or around the corner. Last but not least, a corner profile can also contribute to rainwater getting behind the cladding through the gap. When installing cladding panels with corner profiles, we recommend bonding the aluminium profile to the panel on both sides with an MS polymer and selecting the fixed points of the cladding panels from the corner.
Connecting profiles are very often also called double T-profile or H-profile. The reason for this lies in the view of the cross-section of a connecting profile, which resembles the capital letter H. Such profiles serve the purpose of visually connecting two adjacent facade panels. To do this, the profile is slipped onto an existing facade panel and another panel is inserted in the opposite profile groove. However, the required distance between the panels must always be maintained even when using connecting profiles in order to guarantee the panels the possible expansion space. Otherwise, the panels may bulge unattractively in the event of thermal expansion. Gluing the connecting profile can be advisable, because even with HPL boards there are certain tolerances in the material thicknesses. Although these are usually extremely small, they can contribute to the profile slipping. It should be noted, however, that the profiles should always be glued to a panel on one side only and not to both sides. We recommend a strong assembly adhesive such as our MS polymers for this purpose.
NOTE: If the aluminium profiles are to be mitred, the profile length should always correspond to the edge length.
For the installation of facade cladding, substructures made of wood or aluminium are usually erected. Wood in particular has the disadvantage that the squared timbers are not always completely straight or are slightly twisted, which can make the installation of facade panels more difficult. In addition, wood can rot over time due to surrounding moisture. However, with our aluminium profiles, which we offer in two different versions, these problems do not exist, so that mounting the facade cladding can not only be achieved quickly and easily, but is also extremely durable.
The aluminium profiles are either screwed directly to the wall, resulting in a wall distance of 30mm to the facade panel, which can be lined with additional thermal insulation to optimise the energy efficiency of the building, or fastened with so-called anchor rods. Especially in the case of very uneven masonry walls, an even wall distance can be achieved with threaded bolts. These are screwed into the masonry or, when using impact anchors in concrete, hammered into the drilled hole until the desired wall distance is achieved. The profile is then mounted with a hexagonal nut on the thread. The threaded anchor rods should be chosen to suit the material of the wall. The required length can also be decisive, especially if insulating materials are to be inserted behind the facade cladding in a specified thickness.
Z-profiles, which owe their name to the cross-sectional view, are used on the one hand on the outer sides of the substructure and on the other hand the profiles can also be used excellently when large facade panels are to be fixed where mounting points are provided within the panel surfaces. The contact surface of the profile is 40 mm. This applies both to the mounting surface on the wall side and to the mounting surface of the facade panels. When using the profile as the outer profile of the substructure, it must be ensured that the profile is mounted so that the mounting surface of the facade cladding is mounted to the inner side of the substructure. Otherwise, the edge distance of the panel holes will be too small at around 20mm.
The so-called omega profiles are used when two facade panels adjoin each other. These profiles are also called double profiles or connecting profiles for substructures and have two 40mm wide mounting surfaces with a distance of 60mm from each other. This ensures a sufficient distance between the panels as well as the edge distance of the hole drillings within the facade panels. As with the Z profiles, the profile depth is 30mm, resulting in a wall distance of 30mm, which is very suitable for optional thermal insulation.
TIP: The substructure profiles are not pre-drilled to ensure maximum flexibility during installation and can be easily drilled with our HSS drills.
Facade cladding with substructures made of Z-profiles and omega profiles is very easy to erect. Good planning of the substructure, taking various factors into account, plays a decisive role. In addition to the mounting requirements of the panel material that is to be used as facade cladding, it is also important to take a closer look at the facade to be clad in order to check whether direct wall mounting of the profiles is possible or whether a distance to the wall is necessary. This may be necessary in the case of poorly masoned facades or also in the case of additional thermal insulation.
Before mounting the substructure, the facade to be clad should be checked for the load-bearing capacity of the material. Depending on whether it is hollow sand-lime bricks, hard clinker or concrete, a distinction must be made between the type and number of fasteners for the aluminium profiles. Basically, 8 mm thick threaded bolts are used for the profiles. These have a metric thread of size M8 on the side on which the profile is fastened. The side that is screwed into the masonry, on the other hand, varies according to the type of material. For concrete, impact bolts are usually used, which are hammered directly into the drill hole without a plug. In the case of clinker, sand-lime brick or aerated concrete, the holes are drilled in 10mm and fitted with an appropriate dowel. But be careful, not every dowel is equally suitable for every material. The threaded bolt should then be provided with a coarse thread on the wall side so that it can be screwed well and securely into the plug. The number of fasteners for the substructure depends, on the one hand, on the thickness of the facade panel, because the weight of the facade cladding also increases with increasing thickness. On the other hand, the more porous the substrate, the higher the number of threaded bolts that support the substructure. Consequently, fewer bolts are needed for hard concrete than for sand-lime bricks. Aerated concrete, on the other hand, does not have a high load-bearing capacity, so more screws must be used here than with sand-lime bricks.
In the case of even facades, such as concrete, the aluminium profiles can certainly be attached directly to the facade. In the case of brick facades, especially in old buildings, it is quite possible that the facade is not even due to protruding bricks or clinkers, so that direct screwing into the brickwork is hardly possible. In this case, it is advisable to use bolts with a lock nut or a fixed washer as a thread limit. This allows the wall distance of the profile to be increased to such an extent that a vertical, straight installation of the profile can be made. Depending on how far the wall distance should or must be increased, longer threaded bolts must be used to guarantee a secure hold of the bolt in the masonry. With increasing wall distance, the number of fasteners should also be increased. When installing substructures with wall spacing, it is recommended to extend the installation with diagonal fasteners in addition to the normal fasteners in order to exclude vertical distortion of the substructure due to high weight loads. This can be done either with conventional bolts of sufficient length or with special bolts with brackets.
When facade cladding is installed, it is advisable to provide the intermediate spaces with suitable thermal insulation in order to optimise the energy efficiency of the building. A distinction must be made here as to whether insulation panels are applied to the facade in advance or whether the insulation material is placed between the vertically mounted aluminium profiles afterwards. The material thickness of the insulation material also plays an important role, because with increasing thickness, the wall distance of the substructure also increases, which is accompanied by an increase in the fastening points and longer facade bolts. Here, too, it may be necessary to add diagonally placed fixings to counteract vertical warping.
The surface area of the facade cladding not only plays a role in the required quantity of aluminium profiles, which we offer in two-metre lengths, but also what type of profiles are needed. Especially for wide facade claddings that consist of several facade panels next to each other, the simple Z-profiles are required for the outer sides of the cladding. These are attached in such a way that the support surface for the facade panels faces the inside of the surface of the facade cladding in order to ensure sufficient edge distance of the hole drillings in the facade panels. Where two facade panels are adjacent to each other, on the other hand, omega profiles are used, which have two separate support surfaces at the ideal distance from each other in order to fix both facade panels with an expansion gap to an aluminium profile. If small format facade panels are used, intermediate profiles may not be necessary. In the case of larger panel formats, however, fixings may be necessary between the mounting points on the panel edge, so that here again the simple Z-profiles can be used. It should be noted, however, that the mounting on the wall must be carried out with an offset of 40 mm due to the offset bearing surfaces on the wall and panel. The number of profiles to be used as a substructure and the distance between them depends on the material of the facade panel as well as the thickness of the panel material.
When the substructure has been completely achieved, the facade panels can be mounted. In the case of heavy HPL panels or even heavier fibre cement panels, they are usually fastened with colour-coordinated facade rivets. In the case of aluminium composite panels with facade approval, riveting is also a very safe and quick method, but in some circumstances bonding with an assembly adhesive, such as our MS polymer, may also be possible here. When bonding, pre-treatment with a bonding agent (primer) can significantly improve the bonding. When bonding, however, make sure that the panels are adequately fixed to prevent them from falling down before the mounting adhesive has cured. When riveting, both the panels and the aluminium profiles must be pre-drilled. It is very important that the holes in the panel are transferred exactly to the substructure. It is also important to ensure that one hole of each panel is drilled as a fixed point to match the rivet. The drill diameter for our (and almost all other) facade rivets is 5.1mm. All other holes in the panel are drilled with a diameter between 8mm to a maximum of 10mm. The substructure, on the other hand, is always drilled with the HSS drill in 5.1mm diameter. The advantage of installing with facade rivets is that there is no need for a fixing time, because riveted joints can be loaded immediately.
NOTE: The profiles do not have holes for mounting on the wall, nor do they have holes for mounting the panels with facade rivets. However, these holes can easily be drilled with a standard cordless screwdriver and a metal drill, such as our HSS drills in 8mm or 5.1mm.
Our edge profiles are made of a high-quality rustproof aluminium alloy that is suitable for outdoor use without hesitation and does not require any special care. In the event that they need to be cleaned of dirt caused by weathering, it is sufficient to use warm water with standard household cleaners. When cleaning, however, always make sure that the cleaner is compatible with the facade panel used so as not to impair the appearance of the panel surfaces. For cleaning, we always recommend a soft cotton cloth and no microfibre cloths, as these could cause slight scratches.
Cleaning is unnecessary for the profiles for the substructure, because these are usually completely covered by the facade panels, so that they are no longer visible and therefore no longer accessible for cleaning.
Aluminium is a valuable alloy that can be recycled very well by melting it down as often as desired into new profiles, screws or the like. In the event that you no longer wish to dispose of the remaining pieces of our facade profiles, we recommend that you take them to a recycling centre where the metals are collected and recycled. Depending on the quantity, this can also be done by purchasing them from a scrap dealer, but the sale is only worthwhile if the total weight is greater, so that individual profile remnants are hardly of interest to a buyer.