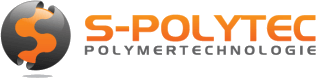
We offer you high-quality tools for plastics processing for a wide range of applications from selected, well-known manufacturers for professional use at favourable prices.
Incl. 19% Tax
Incl. 19% Tax
Incl. 19% Tax
Incl. 19% Tax
Incl. 19% Tax
Incl. 19% Tax
Incl. 19% Tax
Incl. 19% Tax
Incl. 19% Tax
Incl. 19% Tax
Incl. 19% Tax
Incl. 19% Tax
Plastic sheets are rarely used without further processing, so they are usually first cut to the desired size. Drilling, e.g. for fastenings or for the production of perforated plates, is also one of the common methods of preparing plastic sheets for later use, as are milling or laser cutting. As a rule, plastics can be processed with simple tools from the DIY store or specialised trade without the need for special tools or machines. Shaping, edging or bending are also part of the widespread practice to produce prefabricated plastic parts. These mostly thermal processing techniques, on the other hand, usually require more specialised tools, although small hot-forming operations can often also be carried out with a hot-air blower. The welding of plastics is again carried out by applying heat with a welding blower. Here, plastic parts are permanently and securely joined together by fusing with a suitable welding rod.
It is not uncommon for small work steps to be necessary for the preparation or reworking of the respective processing step, which contribute to an optimised result. As a rule, small useful hand tools are sufficient for this. For example, to improve the cutting pattern after sawing or milling, the edges are broken with a deburrer to reduce the sharpness. Deburring holes can also have a positive effect on the final result. Preparatory measures include, for example, the precise marking of drill hole positions. This can often be done with a conventional permanent marker. A scribing needle in the form of a biro is also excellent for marking the drill holes. Depending on the material, a centre punch can also be very helpful to prevent the drill from slipping on hard plastic surfaces such as HPL. Stripping the surfaces before welding plastic parts is another preparatory step that has a positive effect on the welding result.
Once the processing of the plastic is complete, one or the other hand tool can also be very useful for the actual use. If plastic panels are assembled with rivets after drilling, as is often the case with aluminium composite panels or HPL panels, riveting pliers are required, for example, into which the rivet mandrel is inserted to create the riveted joint by squeezing the rivet sleeve.
In our online shop, we offer you not only high-quality plastic sheets in precise cuts for every conceivable purpose, but also suitable assembly material, as well as useful tools for further processing of the plastics.
Plastic sheets can be processed in many different ways. The cutting of plastic sheets is one of the most common processing methods. Especially with machining methods such as sawing, milling or drilling, sharp cut edges can arise due to a fine grade, which can be easily removed with a deburring tool. For this purpose, we offer an extensive selection for the subsequent deburring of edges in our online shop. With the high-quality profile scrapers with replaceable blades, straight cuts can be deburred in no time at all. For holes or rounded corners, as well as small, filigree recesses, our handy quick deburrer with 360° blade is perfect.
When it comes to our deburring tools, we not only rely on renowned manufacturers that stand out for their professional workmanship and quality, but also pay attention to sustainability and durability of the hand tool. For example, we stock profile scrapers with wooden handles and replaceable blades made of a robust metal alloy, which are not only perfect for deburring plastic sheet blanks, but can also be used very well to remove paint, adhesive residues or coarse, hard impurities from flat surfaces. Our handy quick deburrer is also characterised by professional quality and is ideally suited for small deburring of drill holes which can be carried out in no time at all with this useful tool. Thanks to the slim design with clip, the deburring tool is always at hand.
NOTE: When deburring, proceed carefully and avoid great pressure on the blade of the deburring tool to prevent injury or jamming of the deburrer.
The joint repair set consisting of a joint cutter and a squeegee is ideal for removing old joints from skirting boards on tiles, laminate, parquet or natural stone in order to reseal them directly afterwards. The main advantage over removing the joints with a cutter knife is that it is made of robust plastic, which cannot quite compete with the sharpness of a metal blade, but does not damage the usually sensitive surfaces.
The plastic blade pointed on both sides makes it relatively easy to remove the old, brittle or cracked joint. By applying light, even pressure when guiding the tool along the joint, the old sealant can be planned out right into the corners. If small residues of silicone adhere to the flanks of the sealant, this step can certainly be repeated until the silicone has been completely removed. In order to ensure a perfect hold of the new silicone joint to be applied, any last adhering remnants of the old joint should be removed with a liquid silicone joint remover or a household sponge and the joint cleaned afterwards.
The simple plastic joint remover has a preformed geometry made of silicone to which the new sealant to be applied does not adhere and thus enables easy smoothing of the joint. The triangular shape with rounded tip is held at a slight angle when pulling off and is ideal for expansion and connection joints of floor coverings or in sanitary areas. The predetermined angle of the joint puller ensures that a visually appealing joint with an even, perfect smoothing result is achieved without the puller getting stuck in joints of wall and floor tiles.
TIP: The repair set is made of plastic and is therefore ideal for delicate surfaces or for occasional touch-ups and repairs to silicone joints.
NOTE: Before reapplying the sealant, the joint should be completely cleaned of the old silicone to ensure optimum adhesion of the joint.
The care and cleaning of tools after use contributes not least to the service life of a tool. Deburrers or profile scrapers will usually hardly require any special care or cleaning, as long as they are used in accordance with their intended purpose. Chips that have been removed can be easily removed by blowing or using compressed air. For stubborn dirt, however, the use of simple cleaning agents such as water with mild soap can also achieve the desired effect. To avoid corrosion, however, the tools should always be dried thoroughly. In the case of tools made of plastic, such as our joint remover or the joint remover, silicone that has not completely hardened can be removed by rubbing after drying. A silicone remover can be helpful for stubborn adhesions.
Our hand tools for processing plastics and adhesives are made from a wide variety of materials. We always make sure that they are made from sustainable, recyclable materials that are easy to recycle. Whether by using natural materials, such as wood for handles, or plastics that can be excellently processed into recycled plastics by grinding and melting them down. However, due to the large number of different hand tools we offer, we cannot give a general answer on how to dispose of them properly, so this information should always be taken from the respective product.