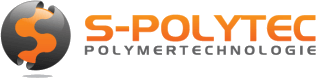
Deep-drawing plastic - creating high-quality and dimensionally accurate moulded parts with the right plastics is not witchcraft if you know how to do it.
Deep-drawing is now a common method of pulling materials in series into three-dimensional shapes using negative pressure. Originally originating from metal shaping, the term deep-drawing is now also used colloquially for the actual thermoforming of plastics.
Regardless of a slightly different working method, deep drawing for plastic offers an ideal possibility for permanent shaping. In combination with the right plastic, durable, dimensionally stable and precise workpieces are created.
Thermoforming, or deep-drawing, of plastics is basically very simple to describe. A plastic sheet is heated to the point of thermal deformability and then drawn over a tool by means of a vacuum. Finally, the plastic is cooled down to below the deformation limit so that it retains the shape of the tool as the final design.
The temperature range for thermoforming the respective plastics depends on the plastic itself. The heating time also depends on the choice of plastic and also varies depending on the thickness of the plastic sheets from which thermoformed parts are to be created.
Depending on the plastics used, plastic workpieces produced by deep drawing can be given different properties. Whether dimensionally stable, flexible, brittle or tough, the plastic used determines the subsequent properties.
ABS plastic is characterised above all by its hardness and impact resistance. Good chemical resistance to non-polar solvents such as petrol or diesel make ABS suitable for a wide range of applications.
The ideal temperature range for thermoforming ABS is between 160°C and 190°C. However, ABS should be dried in an oven before thermoforming, as the plastic absorbs moisture from the environment.
Since ABS plastic per se is not UV and weather resistant, ABS sheets with ASA surfaces offer the possibility of combining the other positive properties of ABS plastic with UV and weather resistance. Thus, these plastics are also suitable for outdoor applications, such as façade cladding.
The ideal temperature range for thermoforming ASA/ABS is between 160°C and 190°C. Similar to pure ABS, pre-drying is also recommended for ASA/ABS to avoid bubble formation during thermoforming.
Go to our plastic sheets made of ASA/ABS
PMMA, or more commonly known as acrylic glass (or the brand name Plexiglas), is a transparent plastic for use in thermoforming. Its high resistance to weathering, UV light and general ageing leads to frequent use in display and enclosure construction, as well as various other indoor and outdoor applications. Its toughness and high scratch resistance make it a viable alternative for real glass.
The ideal temperature range for thermoforming acrylic is between 150°C and 190°C.
To our plastic sheets made of acrylic glass (PMMA)
The strength of polystyrene plastic lies in its ease of processing. Thermal deformability is already achieved at comparatively low temperatures, so that the effort required to create moulded parts by deep-drawing is quite low. This makes polystyrene very suitable for equipment and plant construction. In addition, it is very popular with model makers who also appreciate the simplicity of processing.
The ideal temperature range for thermoforming polystyrene is between 90°C and 140°C.
To our plastic sheets made of polystyrene (PS)
PE, or polyethylene, is a plastic with a particularly high impact strength in the low temperature range. In combination with its good electrical insulating capacity, it is therefore very well suited for various applications in technical areas. Its long service life and slippery surface, on the other hand, also make it easy to use in applications with mechanical movement, for example in furniture construction or for household objects. It should be noted, however, that PE-HD is most suitable for deep drawing.
The ideal temperature range for thermoforming polyethylene is between 160°C and 200°C.
To our plastic sheets made of polyethylene (PE-HD, PE-HMW, PE-UHMW)
Polypropylene is a plastic approved for food and drinking water applications. Its high resistance to chemicals and good resistance to high temperatures make it ideal for countless uses in the catering, kitchen and household sectors. Its temperature limits are 110 degrees Celsius for permanent use and even up to 140 degrees Celsius for short periods.
The ideal temperature range for thermoforming polypropylene is between 190°C and 220°C.
To our plastic sheets made of polypropylene (PP-H, PP-S)
The company S-Polytec is the supplier for plastics of all kinds in Europe. With its own production and as the only dealer with its own large and extensive warehouse for ABS and TüV-certified ASA/ABS in Europe, S-Polytec can react quickly and reliably to customer requests. Customer satisfaction always comes first. Sustainability is not just a zeitgeist here, but an essential component of economic success. 99 percent of the plastic waste produced is recycled into production and thus reused without loss. This saving of valuable raw materials benefits the environment and not least S-Polytec's customers.